Surface Finishes Service
High-quality surface finishing services enhance both the aesthetics and functionality of your parts, regardless of the manufacturing process employed. Select from a variety of suitable surface treatment methods to optimize your plastic and metal production components.
Anodizing is an electrochemical technique used to increase the corrosion resistance and strength of metal surfaces, especially aluminum. This process forms a protective oxide coating by submerging the metal in an electrolytic bath and passing an electric current through it. Additionally, anodizing allows for aesthetic enhancements, as the resulting oxide layer can be colored with a wide range of dyes.

Electroplating is a method where a metal coating is applied to a substrate by using electrical current. This process requires submerging the substrate and a metal electrode in an electrolyte solution, then applying a direct electric current across them. Metal ions from the solution are drawn to the substrate, creating a thin, protective metal layer on its surface. This technique not only improves the substrate’s appearance but also boosts its corrosion resistance and durability.
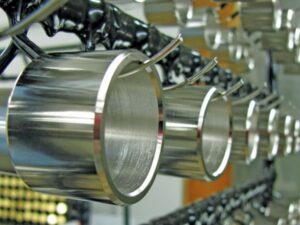
Powder coating is a durable and eco-friendly finishing technique used on metal objects. It involves applying electrostatically charged dry powder onto a grounded metal surface, followed by heating in an oven to melt the powder into a smooth, uniform coating. This process provides excellent resistance to corrosion, chipping, and fading, and is available in various colors and finishes. Powder coating also emits fewer volatile organic compounds (VOCs) than traditional liquid painting, making it environmentally preferable.
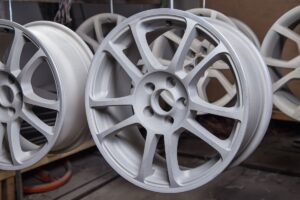
Sandblasting, or abrasive blasting, is a method used to clean, smooth, or texture surfaces by blasting them with fine abrasive particles at high speeds. This process typically uses compressed air or a centrifugal wheel to propel materials like sand against the target surface. Commonly, we employ different grit sizes such as 80#, 100#, 120#, and 150# for sandblasting, which allows for varying degrees of surface refinement. This technique is especially effective in preparing surfaces for painting or coating by removing rust, scale, old paint, and other contaminants.
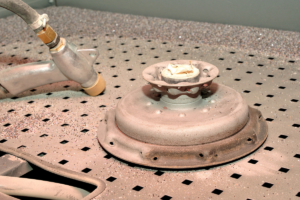
Silk screening, also known as screen printing, is a printing technique used to transfer images or patterns onto various substrates including fabric, paper, plastics, and metals. This process involves the creation of a stencil, or screen, which blocks certain areas to prevent ink from passing through. The screen is positioned over the material, and ink is then pressed through the unblocked areas of the screen to imprint the design onto the substrate beneath.
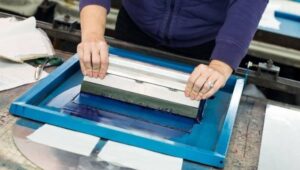
Passivation is a chemical process that enhances the corrosion resistance of metals like stainless steel by removing surface contaminants and promoting the formation of a thin, protective oxide layer. This treatment, often using citric or nitric acid, helps to prevent rust and maintain the integrity of the metal in various harsh environments. Passivation is essential in industries such as aerospace, medical, and food processing, where durability and hygiene are critical.
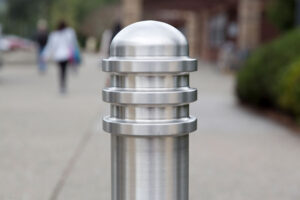
Black oxide coating is a chemical conversion process used to create a black finish on the surface of metals such as iron, stainless steel, and copper. This treatment involves immersing the metal in a bath of oxidizing salts that react with the metal to form a magnetite layer (Fe3O4), which gives the surface a matte black appearance. Black oxide does not significantly alter the dimensions of the part and provides mild corrosion resistance. It is primarily used to reduce light reflection and improve the aesthetic appeal of metal parts, and it also offers some lubrication properties. This coating is commonly found in automotive components, tools, and firearms.
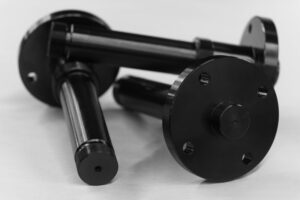
Galvanizing is a process used to protect steel or iron from corrosion by coating it with a layer of zinc. Typically done through hot-dip galvanizing, the metal is submerged in molten zinc, forming a durable barrier that prevents rust. This cost-effective method is widely used to extend the life of metal structures exposed to harsh environments, such as outdoor railings and bridges.
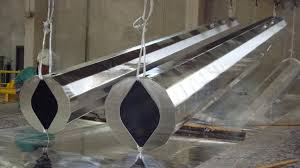
Polishing is a process that smooths and enhances the surface of materials like metal by removing imperfections. It results in a glossy, reflective finish. Mirror polishing, a more refined version, achieves an extremely smooth and highly reflective surface but is more labor-intensive and costly. It is often used for decorative purposes or in applications where visual appeal is important.
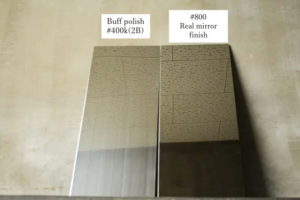
Chrome plating is a surface treatment that involves applying a thin layer of chromium onto a substrate, typically metal or plastic. This process enhances the object’s corrosion resistance, durability, and aesthetic appeal, providing a shiny, reflective finish. It is widely used in automotive, manufacturing, and consumer goods industries to improve both functionality and appearance of various components.
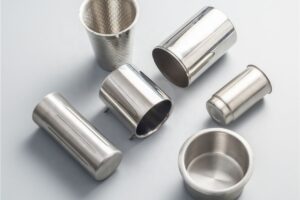