Rapid Injection Molding at AS Prototypes
Introduction to Rapid Injection Molding at AS Prototypes
At AS Prototypes, we specialize in merging injection molding with rapid prototyping to produce high-quality, injection-molded parts through rapid tooling. This technique, known as bridge tooling, allows for the production of up to 100,000 parts using production-grade resins. Ideal for creating end-use prototypes, rapid injection molding delivers parts identical to full production with significantly reduced lead times and costs.
Why Choose Rapid Injection Molding?
Rapid injection molding is perfect for projects requiring end-use prototypes that closely replicate final products in both material and design. It provides a cost-effective, swift transition from prototyping to full production, bypassing the lengthy timelines typical of traditional production tooling.
Rapid Injection Molding Services at AS Prototypes
Our tools are primarily crafted from steel, offering greater durability and a higher part output than aluminum, enhancing both longevity and cost-effectiveness.
Get Started with Your Project
Kick off your project with a free consultation from our expert team. Contact AS Prototypes today to see how our rapid injection molding services can fast-track your prototype or low-volume production, ensuring top quality and efficiency.
Advantages of Rapid Injection Molding at AS Prototypes
Lower Upfront Investment: Requires less initial capital than traditional methods, making it ideal for startups and cost-conscious businesses.
Flexibility: Easily accommodates design changes, supporting dynamic product development and iteration.
Real Production-Grade Materials: Uses the same materials as full-scale manufacturing, ensuring prototypes and low-volume parts are of high functional and performance quality.
High Quality and Speed: Delivers top-quality parts with rapid turnaround, reducing lead times and accelerating market entry.
Applications of Rapid Injection Molding at AS Prototypes
Prototyping: Create realistic prototypes using production-grade materials.
Bridging Prototype to Production: Provides a cost-effective and timely transition from prototype to full production.
Low Volume Production: Ideal for manufacturing small batches, suitable for niche markets or specialized applications.
Market Testing: Test market response with actual production parts.
Rapid Parts Delivery: Quickly produce and deliver parts for immediate needs.
Stay Connected
Follow us on Facebook or LinkedIn for updates and insights on rapid manufacturing. Ready to accelerate your project? Start with fast parts from AS Prototypes.
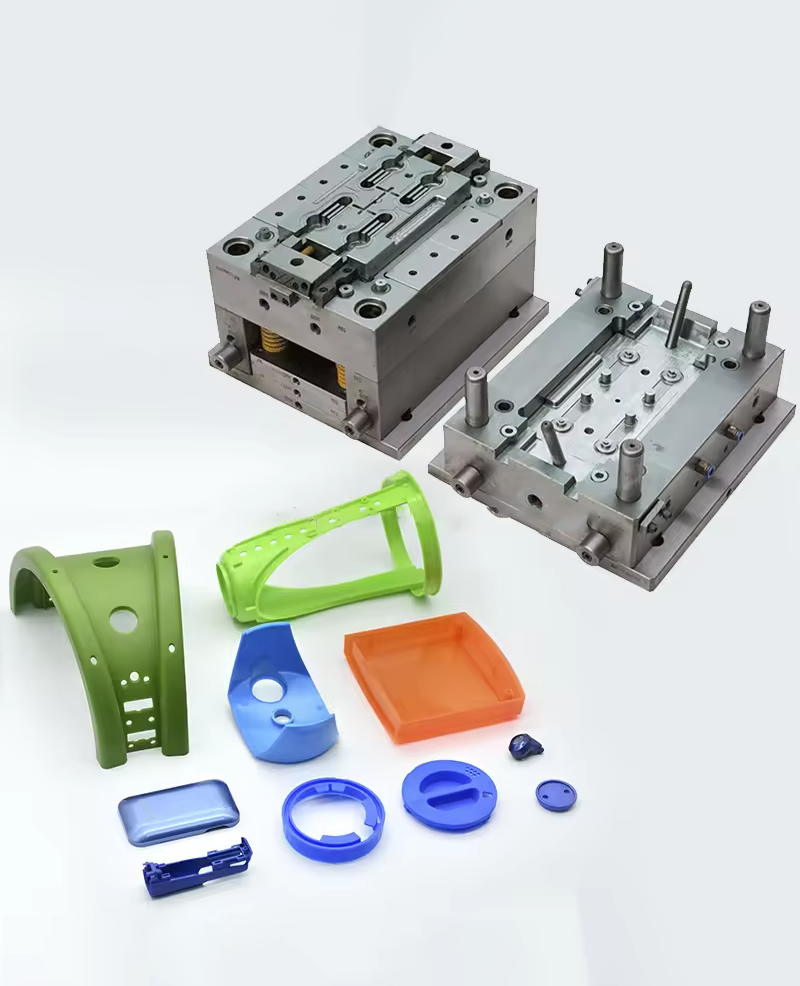
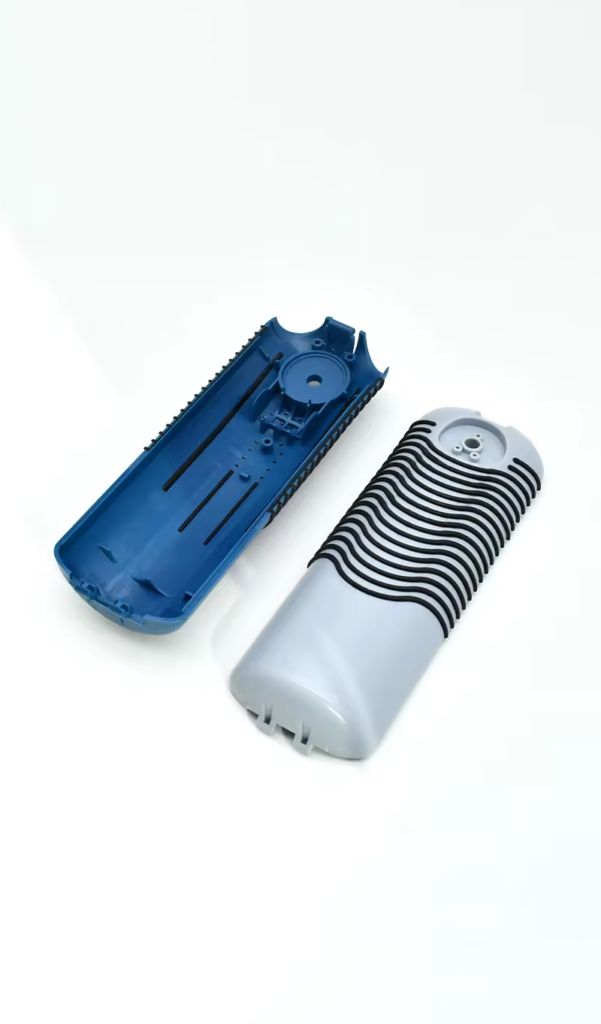
When undertaking rapid injection molding, it’s crucial to optimize the process to save time and costs. Here are streamlined tips for enhancing your rapid injection molding projects:
Surface Finish: Opt for an SPI Finish B-1 with 600 Grit Paper. This finish balances quality with cost-efficiency, minimizing additional processing and reducing both time and expenses.
Design Simplification: Simplify your designs to lessen mold complexity. This reduces the need for sophisticated tooling, cutting costs and shortening lead times.
Modular Tooling: Use modular tooling to combine standardized components for creating complex molds efficiently. This approach can significantly reduce mold production time and cost.
Material Selection: Select appropriate materials for the tool and part. Consider steel for durability and aluminum for faster, more economical tooling.
Early Collaboration: Engage with molding experts early in the design phase to preempt potential issues, optimizing mold design for manufacturability and performance from the outset.
Iterative Testing: Implement iterative testing and prototyping to identify and address issues early, saving time and resources in later stages.
By adhering to these tips and collaborating with experts, you can achieve efficient and cost-effective outcomes in your rapid injection molding projects.
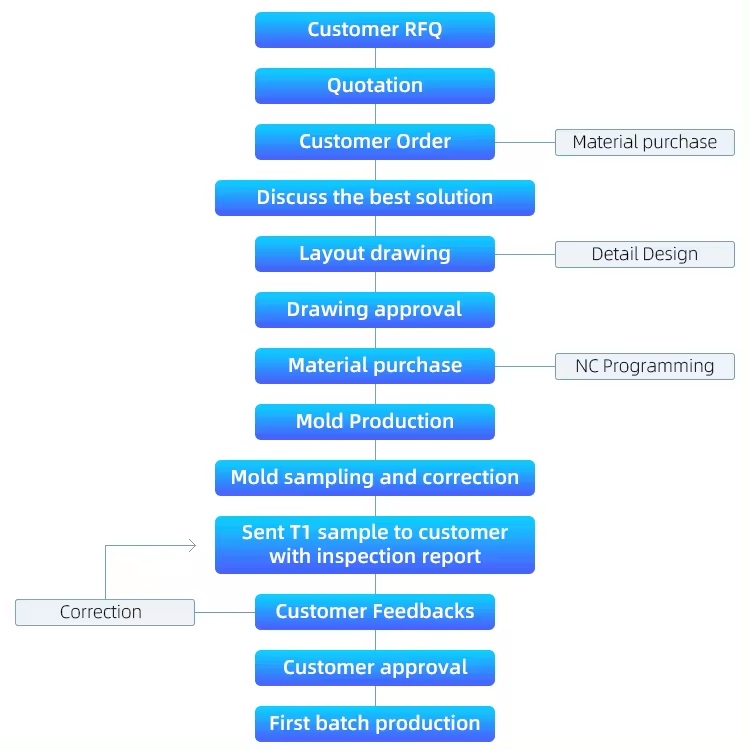