Turning is a machining process where a lathe spins the metal workpiece while a cutting tool moves linearly, cutting away metal to form a cylindrical shape. The angle of the cutting tool can be adjusted to craft various profiles. While traditional lathes require constant manual oversight, modern practices often utilize automated lathes for enhanced precision and efficiency. The predominant form of automation today is Computer Numerical Control (CNC). This discussion delves into CNC turning, exploring its functionality and various applications.
How does CNC turning work?
CNC turning involves the use of a CNC lathe machine where the workpiece is rotated while a cutting tool is moved linearly along its surface. This action systematically removes material from the circumference, shaping the workpiece into a cylindrical form with potential for both external and internal features such as slots, tapers, and threads. CNC turning is adept at operations like boring, facing, grooving, and thread cutting, making it versatile in the production of round components.
In terms of equipment, CNC turning utilizes lathes that are specifically enabled for computer numerical control. These machines can vary from turret lathes, which are useful for quick tool changes, to engine lathes and specialized types designed for specific tasks.
Comparatively, CNC milling machines operate differently. They use rotating cutting tools to engage a stationary workpiece, making them more suitable for complex and intricate parts. In contrast, the stationary tools and rotating workpiece of a CNC lathe allow for quicker and more precise fabrication of cylindrical parts.
To operate a CNC lathe effectively, machinists typically need to undergo specialized training, which includes coursework and certification from an accredited industrial training organization. Training programs for CNC turning cover a range of topics from understanding CNC programming and interpreting CAD files to selecting the right tools and executing proper cutting sequences. Safety protocols are a critical part of the training, emphasizing the importance of safe operation standards.
Initial stages of CNC lathe training may focus on theoretical aspects such as learning command codes and tool selection without immediate hands-on experience. As the training progresses, more practical instruction is introduced, allowing operators to gain direct experience with the machinery.
Turning itself employs single-point cutting tools tailored to specific tasks like roughing, finishing, and threading. Each tool is designed for optimal performance in its respective function, whether it’s for detailed forming, efficient parting, or precise grooving.
Overall, CNC turning represents a sophisticated fusion of traditional machining principles with advanced technology, enhancing the efficiency, accuracy, and range of capabilities in metalworking.
Types of Turning
Turning operations can be categorized into various types, each designed to achieve specific shapes and features on a workpiece:
-
Straight Turning: Also known as cylindrical turning, this process involves reducing the diameter of the workpiece uniformly. It’s commonly used as a preliminary “roughing” operation to remove large amounts of material, setting the stage for more precise machining.
-
Taper Turning: This method creates a cylindrical shape with a diameter that gradually tapers down along the length of the workpiece, useful for forming conical shapes.
-
Spherical Generation: In this process, a program is used to craft a spherical shape around a fixed axis of revolution, or a semicircular tool is employed to reduce the diameter progressively to zero, resulting in a perfect sphere.
-
Grooving: This involves using a specially shaped tool to press into the surface of the workpiece to create a narrow groove or cavity.
-
Parting: This technique involves cutting deeply into the workpiece to separate a finished part from the remaining stock, effectively reducing material waste.
-
Knurling:
This process entails cutting a patterned, serrated texture into the material, often used to enhance grip on the finished part.
-
Threading: Threading involves cutting a helical groove into the workpiece, allowing it to be screwed together with other components.
Each type of turning has its specific applications and is chosen based on the requirements of the final product, ensuring precision and efficiency in the machining process.
What are CNC turning’s applications?
Turning is a machining process that generates rotationally symmetric parts with various features including holes, grooves, threads, tapers, and different diameter steps, as well as contoured surfaces. This method is particularly useful for producing small quantities of custom-designed components like shafts and fasteners, often used in prototype development. Furthermore, turning is commonly employed as a secondary operation to enhance or add features to parts initially shaped by other manufacturing processes, thanks to its capability to achieve high tolerances and superior surface finishes.
While CNC mills are adept at creating complex geometries, CNC lathes excel in producing cylindrical or elongated shapes. CNC turning is favored over milling or 3D printing for its rapid production capabilities, allowing for the efficient replication of identical parts from a single material stock.
The materials commonly used in CNC turning include metals like alloy steel, carbon steel, cast iron, stainless steel, aluminum, copper, magnesium, and zinc. Additionally, the technique is versatile enough to handle plastics and other materials such as ceramics, composites, thermoplastics, and thermosets.
CNC turning machines are highly versatile, making them indispensable across various industries including automotive, electronics, aerospace, firearms manufacturing, sports, and more. These machines can create both simple plane surfaces and complex screw threads, and in the hands of skilled operators using advanced lathes, even intricate three-dimensional products.
The workpiece in a CNC turning operation is usually secured by centers, collets, or clamps, ensuring stability during machining. This process is capable of handling both small and large parts with exceptional precision.
Examples of products manufactured through CNC turning encompass a wide range of everyday and specialized items such as baseball bats, camshafts, bowls, crankshafts, cue sticks, signboards, musical instruments, and the legs of tables and chairs.
Summary
Above, we’ve detailed the CNC turning process and its diverse applications. We hope you have found this information useful. If you’re interested in further exploring industrial processes or need to source CNC turning services directly, consider reaching out to us at AS Prototypes. We specialize in precision machining and can provide tailored solutions to meet your specific needs. For more information about our services or to discuss your project requirements, please visit our website or contact us directly. We look forward to helping you with your manufacturing needs.
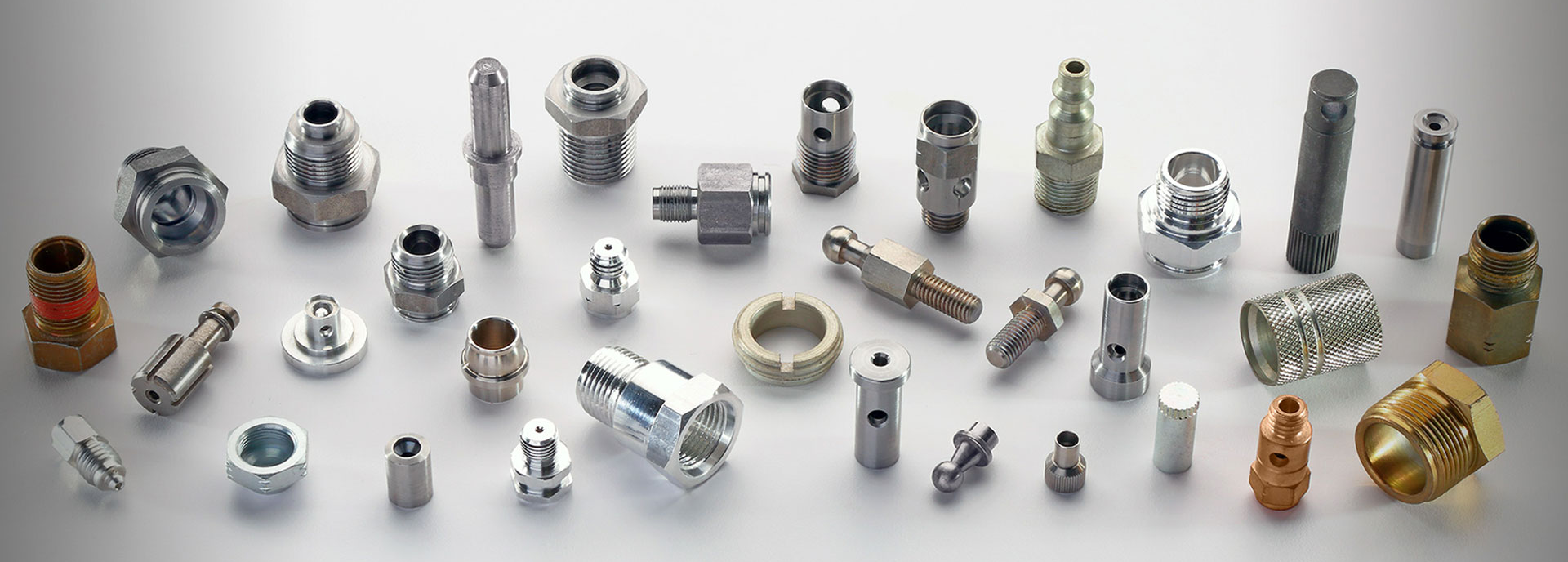