CNC milling, also known as computer numerical control milling, is a precise machining process that utilizes computerized controls along with rotating multi-point cutting tools to methodically remove material from a workpiece. This technique is designed to create custom-designed parts and products and is compatible with a diverse array of materials, including metals, plastics, glass, and wood.
Precision CNC machining services encompass a broad spectrum of capabilities, incorporating mechanical, chemical, electrical, and thermal processes. As a primarily mechanical process, CNC milling operates alongside other machining techniques such as drilling and turning, where material is mechanically excised from the workpiece using the milling machine’s cutting tools.
This overview delves into the CNC milling process, highlighting fundamental aspects, machinery components, and tooling. It also examines various milling operations and discusses alternative machining processes to CNC milling.
Milling Overview
Milling is a machining process that involves the use of cutters to sculpt and shape a workpiece. This is typically done on a movable table, though some milling machines also have movable cutters. Historically, milling was a manual operation performed by skilled workers, but modern practices predominantly use CNC (Computer Numerical Control) milling machines. These machines leverage computer technology to control the cutting tools, enhancing the precision, accuracy, and efficiency of the milling process.
While CNC milling is prevalent due to its superior production capabilities, manual milling still retains relevance in certain contexts. Manual milling requires significant technical skill and experience but can be advantageous for its quicker setup times and lower costs since it eliminates the need for complex programming. This makes manual milling particularly useful for shorter production runs or simpler projects.
Overview of CNC Milling Process
The CNC milling process, a fundamental technique in modern manufacturing, employs computerized controls to guide machine tools that sculpt and modify raw material. This process adheres to standard production phases shared across CNC machining operations, which include:
CAD Model Design: Initially, a part is designed using Computer-Aided Design (CAD) software, producing either a 2D or 3D model based on the project’s needs.
CNC Programming: The CAD model is then converted into a CNC-compatible file format and processed by Computer-Aided Manufacturing (CAM) software. This software creates a CNC machine program that outlines the machine’s operations and the tool paths over the material.
Machine Setup: Preparation of the CNC milling machine involves securing the workpiece to the worktable or a holding device, such as a vise, and mounting the milling tools onto the spindle of the machine.
Milling Operation Execution: The operator starts the program using the machine’s interface, which activates the milling operation. Depending on the application’s requirements, the machine may employ either horizontal or vertical milling configurations, utilizing rotating multi-point cutting tools like mills and drills.
Once the milling process is underway, the cutting tool spins at high speeds, often reaching thousands of revolutions per minute. The machine can manipulate the workpiece in several ways to achieve the necessary cuts:
- Feeding the workpiece into the stationary, rotating tool,
- Moving the tool across a fixed workpiece,
- Coordinating movement between both the tool and the workpiece.
Unlike manual milling, CNC milling typically involves moving the workpiece in conjunction with the rotation of the cutting tool, a method known as climb milling. Conversely, moving the workpiece against the direction of the tool is known as conventional milling.
Milling is frequently used as a secondary or finishing process to add precision to or create features on a part that has been previously machined. These features might include holes, slots, and threads. It can also be used to entirely shape a raw material into the final part. Initially, the tool removes small chips from the workpiece to approximate its shape. Subsequent passes refine the part to high precision and exact specifications. Complex parts may require multiple passes and machine setups.
After milling, the part undergoes finishing and post-processing to meet the designed specifications, completing the production cycle.
CNC Milling Machine Operations
CNC milling is a precise machining technique ideal for creating high-accuracy parts with tight tolerances in prototype, one-off, and small to medium batch productions. Typically, parts are manufactured with tolerances between +/- 0.025 mm (approximately +/- 0.001 inches) and +/- 0.125 mm (approximately +/- 0.005 inches), although some mills can achieve even tighter tolerances of +/- 0.013 mm (approximately +/- 0.0005 inches) or better. This method’s adaptability makes it applicable across various industries and suitable for producing diverse part features such as slots, chamfers, threads, and pockets. Common types of CNC milling operations include:
Face Milling
Face milling involves milling operations where the cutter’s axis of rotation is perpendicular to the workpiece’s surface. This method uses face milling cutters with teeth on both the periphery and the face of the tool. The peripheral teeth are mainly for cutting, while the face teeth are used for finishing. Face milling is typically employed to create flat surfaces and contours, offering superior finishes compared to other milling methods. It can be performed on both vertical and horizontal milling machines. This process includes variations like end milling and side milling, which utilize end and side milling cutters, respectively.
Plain Milling
Also known as surface or slab milling, plain milling involves operations where the cutter’s axis is parallel to the workpiece’s surface. It utilizes plain milling cutters with peripheral teeth that execute the cutting. The choice between narrow and wide cutters depends on the required depth of cut and the size of the workpiece. Narrow cutters make deeper cuts, whereas wider cutters handle larger surface areas. For extensive material removal, a coarse-toothed cutter with slow speeds and fast feeds is first used to rough out the part’s basic shape. Subsequently, a finer-toothed cutter with faster speeds and slower feeds refines the details.
Angular Milling
Angular milling, or angle milling, involves the cutter’s axis being angled relative to the workpiece’s surface. This type of milling uses single-angle milling cutters designed to produce specific angular features like chamfers, serrations, and grooves. Angular milling is often used to create dovetails using cutters angled at 45°, 50°, 55°, or 60°, depending on the dovetail design.
Form Milling
Form milling is used for milling operations involving irregular surfaces, contours, and outlines on parts with both curved and flat sections or entirely curved surfaces. Specialized formed milling cutters or fly cutters, such as convex, concave, and corner rounding cutters, are employed based on the specific application. Common uses of form milling include producing hemispherical and semi-circular cavities, beads, contours, and complex designs in a single machine setup.
Other Milling Machine Operations
In addition to the common milling operations, milling machines are versatile enough to perform a range of specialized tasks. Here are some examples of other milling machine operations:
Straddle Milling: This operation involves the simultaneous milling of two or more parallel surfaces of a workpiece using two cutters mounted on the same arbor. The cutters are positioned on either side of the workpiece, allowing both sides to be milled in one pass.
Gang Milling: Gang milling is the process where multiple cutters of different types, shapes, or sizes are mounted on the same arbor to perform diverse milling operations simultaneously. This method can produce complex parts efficiently by combining different milling processes in a single pass.
Profile Milling: In profile milling, the tool paths are designed to follow a vertical or angled contour of the workpiece. This operation uses cutters that are oriented parallel or perpendicular to the surface of the workpiece to create detailed profiles and features.
Gear Cutting: Gear cutting is a precise milling operation where involute gear cutters are used to form the teeth of a gear. These cutters come in various shapes and sizes, tailored to the gear’s specifications. Additionally, gear teeth can also be machined using specialized lathe cutter bits.
Additional Machining Processes: Milling machines are not limited to milling alone; they can accommodate a variety of other machining tools. This allows them to perform additional operations such as drilling, boring, reaming, and tapping, making them highly adaptable for complex manufacturing tasks.
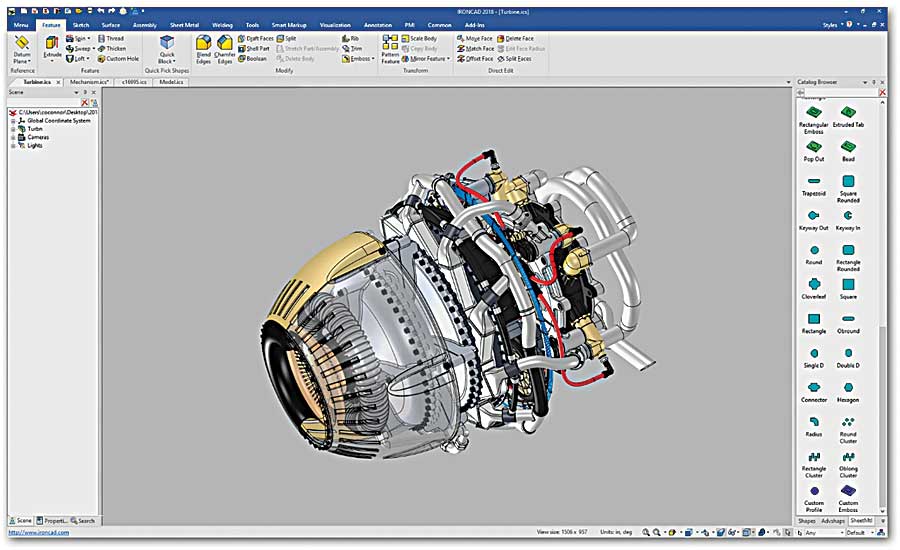
CNC Milling Support Software
Integral to CNC machining, the milling process begins with the use of CAD (Computer-Aided Design) software to create the initial design of the part. Following this, CAM (Computer-Aided Manufacturing) software is employed to develop the CNC programming that dictates the machine’s operations. This program is then uploaded into the selected CNC milling machine to start and carry out the milling operation.
Milling Machine Considerations
Milling machines are generally classified into vertical or horizontal configurations, and also distinguished by the number of axes they operate along.
Vertical milling machines have a vertically oriented spindle, whereas horizontal milling machines feature a horizontally oriented spindle with arbors that enhance support and stability during operations. Horizontal machines are well-equipped for using multiple cutting tools simultaneously, which is advantageous in processes like gang milling and straddle milling. The control systems of these machines vary, depending on the specific model; some allow for the spindle to be moved up and down or the worktable to be shifted laterally, while others feature stationary spindles with worktables that can move in multiple directions, including horizontally, vertically, and rotationally.
When choosing between vertical and horizontal mills, considerations include the nature of the milling tasks, such as the number of surfaces to be milled and the physical characteristics of the workpiece. For instance, heavier and larger workpieces are typically more suited to horizontal milling, whereas tasks like die sinking are more compatible with vertical milling. Additionally, there are accessories available that can adapt a machine to perform functions typical of the other type (vertical or horizontal).
CNC milling machines commonly offer between 3 to 5 axes of motion, enhancing their capability to execute complex cuts and detailed work. The X-axis and Y-axis control horizontal movements (side-to-side and forward-and-back, respectively), the Z-axis manages vertical movements (up-and-down), and more advanced models may include additional axes like the W-axis, which allows for diagonal movements across a vertical plane. Basic CNC mills operate along two axes (X and Y), but more sophisticated models can include up to 5 axes, adding significant versatility to the machine’s functionality. The table below summarizes the characteristics of milling machines based on their axes of motion.
Number of Axes | Characteristics |
3 Axes |
|
4 Axes |
|
5 Axes |
|
In various types of milling machines, either the tool, the worktable, or both elements can be mobile. Typically, dynamic worktables can traverse the XY-axes and also adjust vertically for depth of cut or pivot along the vertical or horizontal axis to expand the cutting range. For milling operations that require dynamic tooling, the machine tool not only rotates but also moves across multiple axes. This movement allows the tool’s side, not just its tip, to engage with the material. CNC milling machines that offer more axes of movement provide enhanced versatility and enable the production of more complex parts.
Types of Milling Machines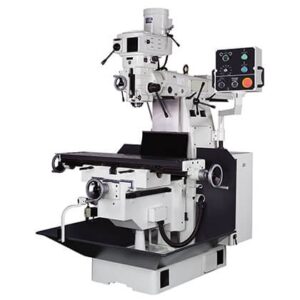
There are various milling machines designed to meet different machining needs. These machines can be categorized based on their configuration, number of motion axes, and specific features. The most prevalent types of milling machines include:
Knee-type:
Knee-type milling machines feature a vertically adjustable worktable resting on a saddle that is supported by a knee. The spindle is fixed, and the knee can be adjusted vertically along the column to position the machine tool. Common examples are the floor-mounted and bench-type plain horizontal milling machines.
Ram-type:
Ram-type milling machines have a spindle mounted on a movable housing, known as the ram, which is attached to the column. This setup allows for movement along the XY axes. Popular variants include the floor-mounted universal horizontal and swivel cutter head milling machines.
Bed-type:
In bed-type milling machines, the worktable is fixed directly to the machine bed, restricting movement of the workpiece along the Y-axis and Z-axis. The cutting tool moves across the XYZ axes. Variations include simplex, duplex, and triplex milling machines. Simplex models feature a single spindle moving along the X or Y-axis, duplex models have two spindles, and triplex models include three spindles (two horizontal and one vertical) to facilitate machining across multiple axes.
Planer-type:
Planer-type milling machines resemble bed-type machines but with a fixed worktable along the Y and Z axes and spindles that move along the XYZ axes. These machines can accommodate multiple tools simultaneously, often up to four, which helps in reducing the production time for complex parts.
Specialized Milling Machines:
Specialized milling machines include rotary table, drum, and planetary types. Rotary table machines feature a circular worktable that rotates around the vertical axis and have tools at various heights for different machining stages. Drum milling machines, similar to rotary table types, have a drum-shaped worktable that rotates horizontally. Planetary milling machines keep the worktable stationary while machining cylindrical workpieces; the rotating tool cuts internal and external features, such as threads.
Summary
The details provided above give an overview of the CNC milling process, including the various operations involved and the equipment necessary for these operations. They also cover key considerations for manufacturers and machine shops when evaluating the suitability of CNC milling for specific machining needs.
For those seeking expert CNC milling services, AS Prototypes stands as a premier provider in the industry. As a dedicated factory, we specialize in custom manufacturing solutions tailored to meet the unique requirements of each client. At AS Prototypes, we pride ourselves on our state-of-the-art technology and skilled team, capable of delivering high-quality, precision-engineered parts. For more information on how AS Prototypes can assist with your CNC milling and custom manufacturing needs, please contact us directly. We are here to help you achieve your project goals with efficiency and precision.