AS Prototypes excels in vacuum-urethane casting technology, enabling the creation of precise silicone rubber molds for producing urethane cast parts in the shortest time. Our cast urethane process is ideal for testing pre-production parts, assessing functionality, and verifying the design of any silicone rubbers.
1.What Is Silicone Rubber?
Silicone rubber is an elastomer composed of silicone—a polymer that includes silicon, oxygen, hydrogen, and carbon. Due to its excellent chemical and physical properties, silicone rubber is widely used across various industries. It is typically stable, non-reactive, and capable of withstanding extreme conditions and temperatures. Silicone rubber can endure temperatures up to +250°C, where most plastics would melt, and remain flexible at temperatures as low as -70°C. Additionally, it has very low toxicity and no detectable odor.
Thanks to these outstanding properties, silicone rubber offers the following benefits:
- Excellent electrical insulation
- Superior sealing capability
- Long service life
- Cost-effective and rapid manufacturing
- Versatility in molding into different shapes
2.Why A Silicone Rubber Mould?
When silicone is in liquid form, it can be stabilized in any environment, allowing the mold to maintain its shape under high load and high temperatures. Once molded, silicone rubber does not shrink because there are no extracts or leachates released after it takes shape. It is widely chosen for mold making due to its excellent reproduction of fine details, physical strength, versatility, ease of use, and availability. Additionally, silicone rubber can be produced in a wide range of colors and hardness levels, making it the material of choice for an increasing number of molding applications.
3.How Is Silicone Rubber Moulding Carried Out?
Silicone rubber moulding is carried out using a series of steps which are discussed as follows;
3.1 Creating the master pattern
The first step in the duplication process is creating the master pattern. At AS Prototypes, we utilize advanced rapid prototyping technologies such as 3D printing and CNC machining to create the master pattern. These modern methods are faster, more cost-effective, and more reliable compared to traditional techniques available in the market.
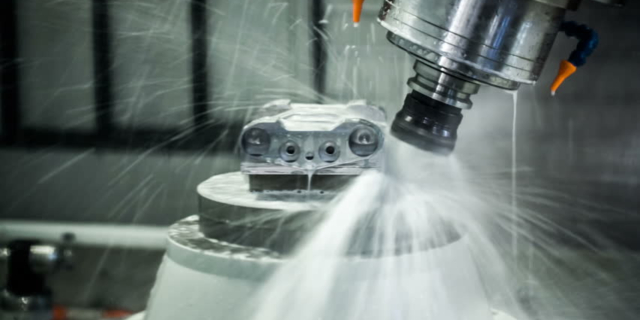
CNC rapid prototyping is done to make the master pattern
3.2 Designing the mould
3.2.1 The setup
Before creating the mold, gating and venting must be carefully considered. Vents and gates are essential for allowing the casting material to flow into the silicone rubber mold. The location and size of the gates are determined by the shape and volume of the master pattern. Generally, the larger the volume of the master pattern, the larger the gate area needs to be.
3.2.2 Choosing the silicone rubber
The silicone rubber used today for the molding process comes in two types: 1) condensation cure (tin-based) and 2) addition cure (platinum-based). Each type has slightly different characteristics and properties. When selecting the appropriate silicone rubber for your mold, one of the most important considerations is the silicone rubber’s resistance to inhibition. Inhibition occurs due to contamination present in or on the master that is to be molded. To address this, a patch test should be conducted prior to the molding process to identify and remove any contaminants.
3.3 Making the silicone rubber mould
Once the master pattern is created, a silicone rubber mold can be produced. A key attribute of silicone rubber is its high reproduction accuracy, allowing it to capture extreme levels of detail. There are two primary configurations commonly used to create silicone rubber molds.
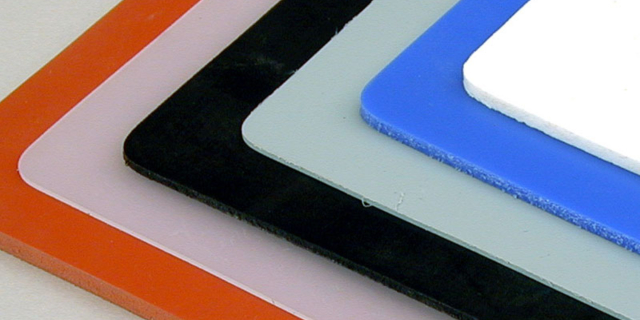
3.3.1 Book mould/single stage mould
The book mold, also known as the single-stage mold, is one of the most commonly practiced silicone rubber molding techniques. In this method, the master pattern is suspended inside a mold box. Liquid silicone rubber is then poured into the box until it is completely filled. After the silicone has cured, the mold is cut open in half. This technique is both cost-effective and time-efficient for creating silicone molds.
3.3.2 Two-part mould/multi-stage mould
This method is somewhat more labor-intensive; however, it offers better control over the mold parting line and enhances the stability of molds, making it suitable for larger parts. The two-part mold is created by establishing a parting line with modeling clay. Silicone is then poured into the mold box, filling it halfway. After the first half has cured, the mold is inverted, and the clay used for the parting line is removed. The frame is then repositioned, and the second half of the mold is poured and allowed to cure.
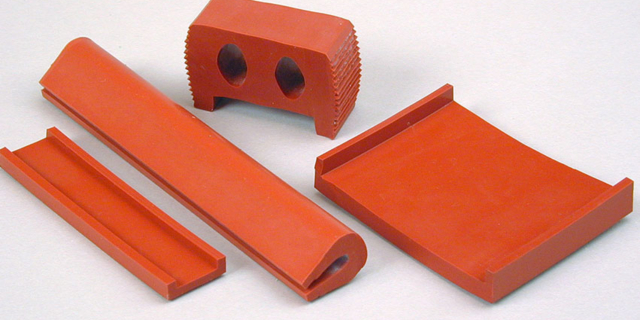
3.3.3 Mixing and de-airing
After selecting the type of mold and silicone rubber, it is crucial to accurately weigh the two components (catalyst and silicone base) to ensure design precision. Mixing should be done in a plastic container that is at least three to four times larger than the volume of the material. This extra space allows air bubbles to escape freely during the de-airing process. Any bubbles remaining in the silicone rubber can negatively impact the integrity of the final product.
4.Applications Of Silicone Rubber
Due to its excellent physical and chemical properties, silicone rubber is a preferred material for a wide range of industries and applications, including:
- Aerospace industry
- Construction & restoration
- Defense industry
- Medical industry
- Plugs
- Sealing gaskets
- Silicone O-rings
- Wire and cable jacketing
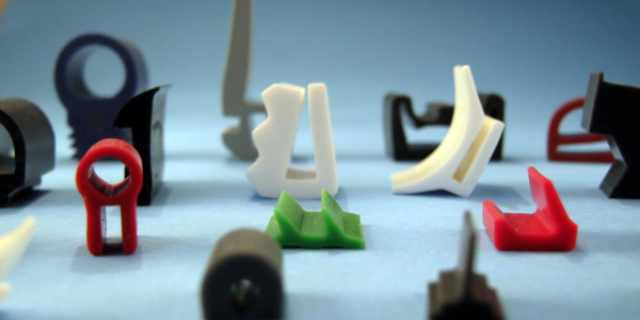
5.We Are Silicone Rubber Moulding Pioneers!
AS Prototypes is proud to have been a pioneer in the creation of silicone rubber molds for over a decade. One of the key factors that give us an edge over our competitors is our commitment to continuous improvement in all phases of mold manufacturing. Silicone rubber molding presents numerous challenges due to the complexity of the process and the high precision required for each mold. At AS Prototypes, we ensure that despite the demanding designs and requirements, we remain agile to deliver top-notch quality prototypes to our valued customers.
Our highly experienced staff and engineers are always ready to transform your complex 3D virtual prototypes into profit-generating products using our state-of-the-art machines and unparalleled skills. No matter which industry you belong to, if you need a silicone rubber molding job done quickly and affordably, AS Prototypes is your answer!