CNC machining tolerances are critical for ensuring the precision required in manufacturing parts across industries. At AS Prototypes, we focus on delivering parts that meet stringent specifications, essential for their form, fit, and function. Here’s how we handle the complexities of CNC machining tolerances to ensure optimal performance and consistency.
The Importance of CNC Machining Tolerances
CNC machining tolerances define the permissible variations in a part’s dimensions. These tolerances are crucial for ensuring that parts fit perfectly within an assembly and function as intended. At AS Prototypes, we use a “±” symbol to denote these tolerances, ensuring that each part meets rigorous quality standards.
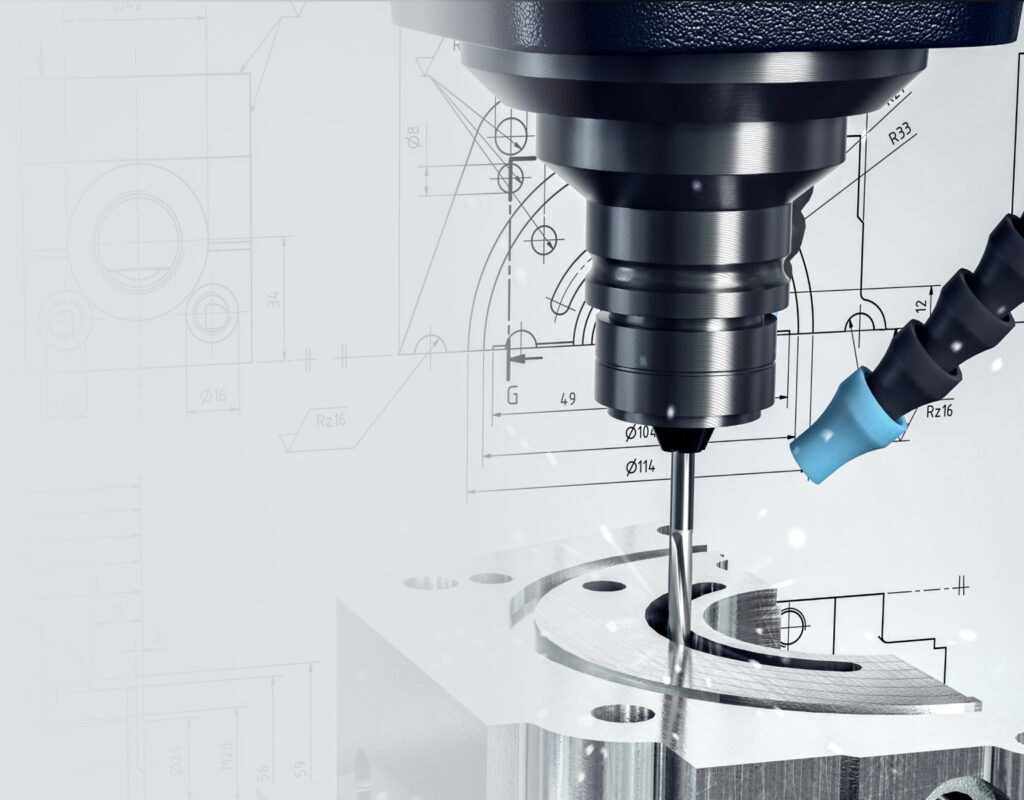
Tolerances in Manufacturing at AS Prototypes
Our approach to CNC machining involves various tolerance types to accommodate different needs:
- Standard Tolerances: We typically work with CNC milling tolerances of about +/- 0.1mm, adhering to standards set by organizations like ASME, ANSI, and ISO.
- Limit Tolerances: These are used to specify a range within which parts must fall to be considered acceptable.
- Unilateral and Bilateral Tolerances: These tolerances allow variations in one direction or both, ensuring that parts are neither too big nor too small.
- Geometric Dimensioning and Tolerancing (GD&T): This system helps in maintaining the geometric properties and dimensional accuracies of parts, which is crucial for complex components.
Processes | Tolerance Standards |
Milling (3-axis) | ± 0.13 mm or 0.005” |
Milling (5-axis) | ± 0.13 mm or 0.005” |
Lathe | ± 0.13 mm or 0.005” |
Router | ± 0.13 mm or 0.005” |
Router (Gasket Cutting Tools) | ± 0.762 mm or 0.030” |
Engraving | ± 0.13 mm or 0.005” |
Screw Machining | ± 0.13 mm or 0.005” |
Steel Rule Die Cutting | ± 0.381 mm or 0.015” |
Rail Cutting Tolerances | ± 0.762 mm or 0.030” |
Surface Finish | 125RA |
Factors Influencing CNC Machining Tolerances
Several factors affect the tolerances achievable in CNC machining:
- Material Properties: The hardness, abrasiveness, and heat stability of materials can influence the final tolerance achievable.
- Machining Processes: Different processes and machine capabilities dictate the precision of the final parts.
- Surface Finishes: Post-machining treatments can alter dimensions, which is why we carefully select surface finishes to maintain tolerance integrity.
- Machining Expertise: The skills of our machinists play a vital role in achieving the desired tolerances. Their expertise in selecting the right tools and setting optimal machining parameters is crucial.
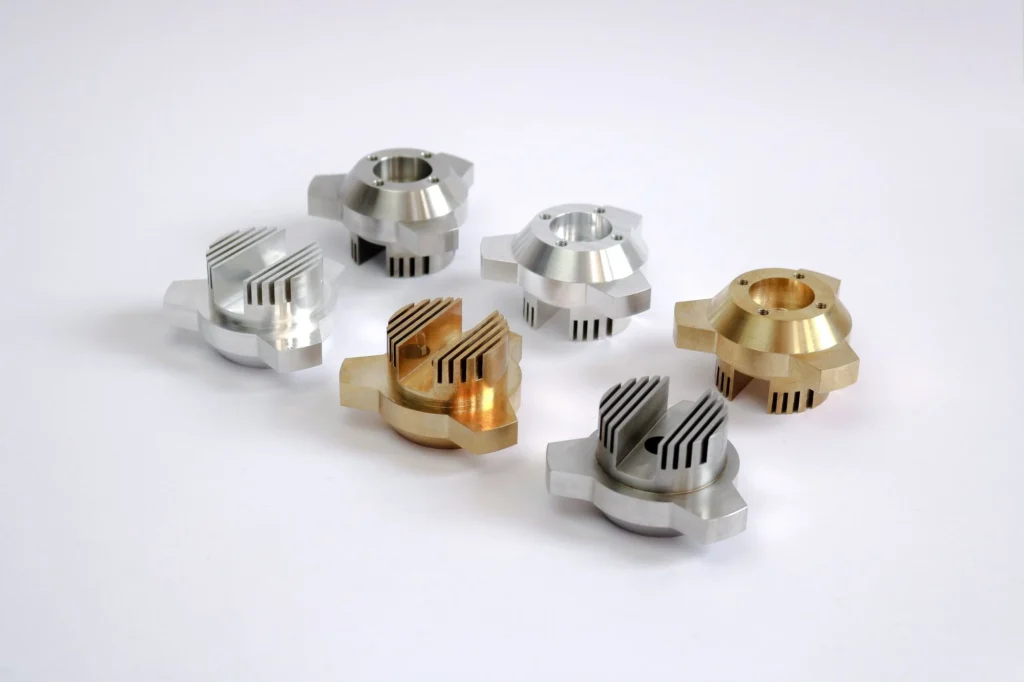
Why Choose AS Prototypes for Precision CNC Machining?
At AS Prototypes, precision is paramount. Our advanced CNC technology and skilled team ensure that your parts are manufactured to exact specifications, supporting industries that require high precision such as aerospace, medical, and automotive. We offer comprehensive services from 5-axis machining to various surface finishing treatments, ensuring each part meets its functional requirements without unnecessary cost inflations.
Partner with AS Prototypes for Your CNC Machining Needs
Choose AS Prototypes for a partnership where precision engineering meets cost efficiency and quality. Our commitment to maintaining stringent CNC tolerances ensures that your projects are successful from the start. Contact us today to discuss how we can bring precision and reliability to your next project.