Transformers from the Movies Are Coming to Life
Many people are captivated by the blockbuster movie “Transformers,” drawn in by the cool and powerful imagery of these iconic robots. Their fighting prowess and dynamic presence ignite the imagination and excitement of viewers. These Transformers open up endless possibilities in the realm of science fiction. While real-life Transformers don’t exist, advancements in high-tech are bringing similar concepts closer to reality.
With continuous technological improvements, formidable robots are no longer just the stars of sci-fi films. These powerful and technologically advanced robots are becoming a part of our everyday lives, blending explosive strength with cutting-edge innovation.
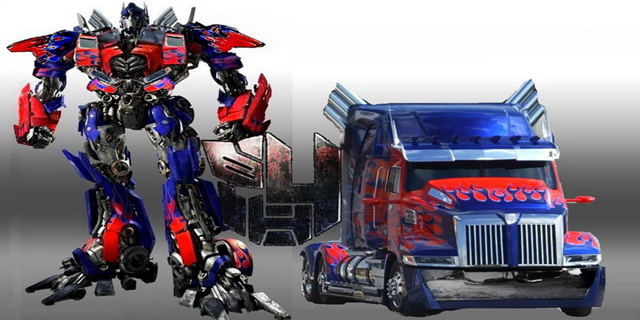
Japanese Company Brings Transformers to Life
“Transformers,” the beloved animated series and Hollywood blockbuster, has captured the hearts of teenagers worldwide. Many of them proudly display “Car People” toys at home, inspired by these iconic characters.
In an exciting development, Japanese companies have spent three years creating functional cars that transform into rideable, variable-size robots. This ambitious project, spanning 15 years and overcoming numerous technical challenges, has finally succeeded.
Meet the J-deite Ride, a four-meter-high transforming robot developed by Asratec Corp., a robot software company affiliated with the SoftBank Group. This remarkable machine features 49 joints throughout its aluminum alloy frame. It can transform from a car to a humanoid robot and back, with people able to sit inside in both modes. The robot can be controlled manually from the cockpit or remotely via wireless or wired connections.
The car form measures 4 meters in length and 1.4 meters in height, accommodating two passengers. In just one minute, it can transform into a 3.7-meter-tall, 4.2-meter-wide humanoid robot. The car has a theoretical speed of 60 kilometers per hour, while the robot can walk at 30 kilometers per hour, controllable via wireless remote. This innovative vehicle is intended for amusement parks, sparking the imagination and setting a precedent for future applied technology.
Did you know that all the parts of this Transformer can be processed using CNC machining? Discover the fascinating relationship between CNC milling services and Transformers in China.
A Chinese Father Creates Transformers
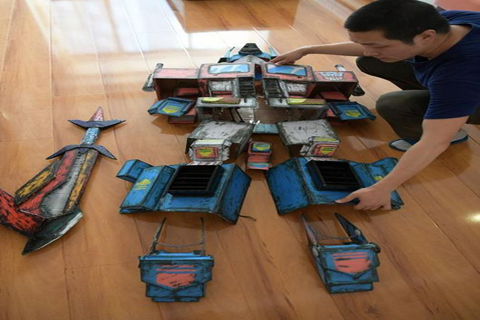
In Xi’an, China, a devoted father has crafted “Transformers” armor for his son, bringing the beloved characters to life in a unique and personal way.
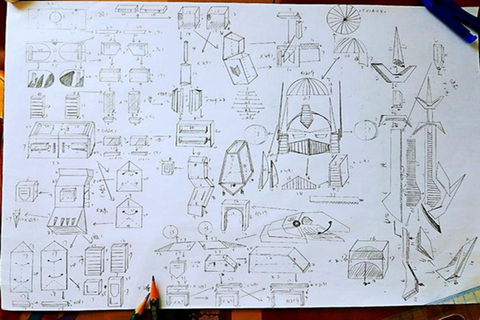
China is home to numerous CNC machining factories capable of turning your creative ideas into reality. With detailed drawings and concepts, these factories can manufacture and assemble individual parts to create a complete Transformer. This remarkable process showcases the power of CNC machining in transforming imaginative designs into tangible creations.
Chinese Farmer Creates Transformers
In China, ingenuity knows no bounds. A farmer from Henan, inspired by the movie “Transformers,” embarked on a personal quest to create his own version of these iconic robots. Despite the long and challenging process, which required a vast array of materials and precise CNC milling calculations, he remained undeterred. His dedication even led to conflicts with his wife, who urged him to abandon what she saw as a crazy idea. Yet, within a year, he successfully completed his Transformer.
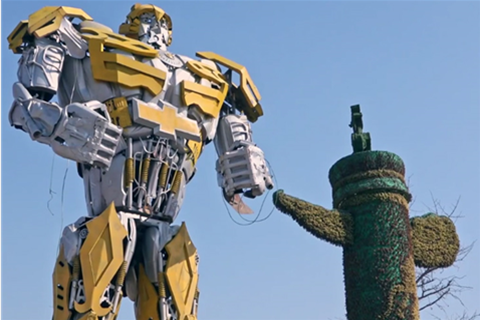
China is home to numerous CNC machining factories capable of producing Transformers. These factories can meticulously craft products to meet strict dimensions, rigorous designs, and varied material requirements, turning creative visions into reality.
CNC Machining
In today’s world, more and more people are starting to embrace the reality of modern manufacturing processes. Have you ever wondered how auto parts are made? The various components of a car, including its body, engine parts, and even the smallest elements, are often crafted using CNC machining. After machining, these parts are meticulously painted to achieve the final look.
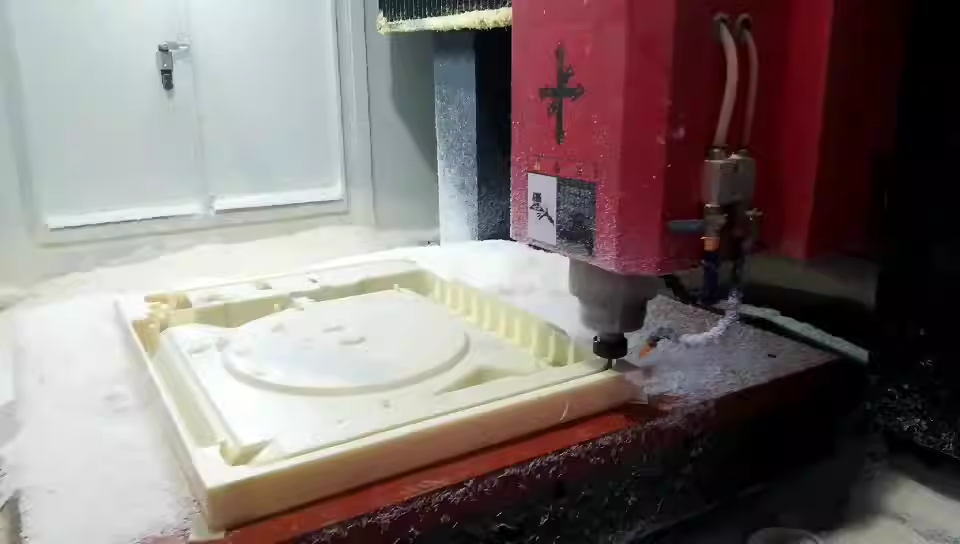
Understanding CNC Machining: The Future of Auto Parts Manufacturing
Computer Numerical Control (CNC) refers to an automated machine that operates based on a programmed set of instructions. By integrating advanced technologies such as computer-aided design (CAD), auxiliary manufacturing, and digital control, CNC machines can transform a block of material into complex three-dimensional parts.
The CNC machining process begins with a three-dimensional data model created on a computer. This model guides the machining center’s tools to cut and shape the material with precision. Once the workpiece is clamped, the digital control system takes over, automatically selecting and changing tools, adjusting spindle speeds, feed rates, and tool paths. This automation allows for the completion of multiple processes on a single workpiece without operator intervention.
In CNC lathe processing, determining the machining routes follows these key principles:
- Ensure Accuracy and Surface Quality: The machining process must guarantee the workpiece’s precision and surface finish.
- Optimize Processing Routes: Minimize the machining path to reduce idle time and enhance efficiency.
- Simplify Numerical Calculations: Streamline the processing procedure by reducing the complexity of numerical calculations.
- Utilize Subroutines: For frequently reused programs, implementing subroutines can simplify the process.
By adhering to these principles, CNC machining enhances efficiency, accuracy, and repeatability in auto parts manufacturing.
2.1 Advantages of CNC Machining in Auto Parts Manufacturing
- High Dimensional Stability and Accuracy: CNC machining offers exceptional dimensional stability, high processing accuracy, and repeatability. The size control achieved with CNC machining surpasses that of existing Rapid Prototyping (RP) technologies.
- Wide Selection of Materials: CNC machining can process almost all engineering plastics and metal materials using a universal milling machine. This ensures consistency between prototype materials and mass production materials.
- Superior Surface Finishes: CNC machined parts boast high-quality surface finishes. After processes like grinding, polishing, and surface treatment, the results can be comparable to, or even exceed, those of open mold products.
- Continuous Operation and High Efficiency: CNC machines can operate continuously 24 hours a day, significantly enhancing processing efficiency.
- Cost-Effective for Small Batches and Large Parts: Compared to RP technology, CNC machining is more economical for producing small batches or large-sized parts.
2.2 What are the disadvantages of CNC?
- Structural and Machine Travel Limitations: CNC parts may need to be spliced into integral components after block processing due to limitations in the machine’s travel and part structure.
- Tool Geometric Constraints: The Z corners of the workpiece will have rounded edges due to the geometric limitations of the CNC tools, necessitating manual post-processing to clean up these areas.
- Complex Data and Path Design: CNC machining requires meticulous data processing, path design, and fixture design. The workpiece often needs to be repositioned multiple times, and step-by-step processing can introduce human error.
- High Labor Costs: The labor costs associated with skilled programmers and operators for CNC machines are relatively high.
2.3 Background of China prototype Industry
With the increasingly fierce competition in the market and the growth of the industrial design industry, prototype companies in China are now focusing on both product model production and industrial design. Verifying the development quality and actual effect of a product requires a hand-plate model. This necessity has led to the emergence of the hand model industry as an independent and flourishing sector within the prototyping and industrial design process.
Many professional prototype model companies have emerged, and larger enterprises, as well as industrial design firms, have established their own prototype model departments. The prototype model industry, often referred to as the “future sunrise industry,” has several advantages:
- High Social Demand: The demand for prototype models is large due to increased investment in product research and development by companies. Additionally, the growth of the domestic social economy indirectly boosts this demand.
- Quality Verification: Hand-plate models are essential for verifying the development quality and actual effects of new products, ensuring that design concepts translate effectively into tangible results.
The prototype model industry is poised for significant growth, driven by the need for precise and reliable product development tools.
Conclusion
AS Prototypes leads the custom manufacturing industry in China, offering a wide range of services such as rapid prototyping, 3D printing, CNC milling, vacuum casting, and injection molding. Our advanced CNC machining ensures high precision, material versatility, and superior surface finishes, making us a reliable partner in product development. Despite challenges, our commitment to quality and efficiency positions us at the forefront of the growing prototype model industry, meeting the increasing demand for high-quality, custom manufacturing solutions.