High-speed milling is neither a recent development nor an entirely new technique. It has been widely used across various industries for many years. For instance, the mold manufacturing industry has utilized high-speed milling for decades. Initially, it was perceived as a niche process involving small tools and high-spindle speed machines. However, today, high-speed milling boasts a much broader range of applications.
In recent years, aluminum alloy has emerged as the most widely used non-ferrous metal structural material in the industry. Consequently, the aluminum alloy industry has matured into a well-established market. So, what exciting possibilities arise when aluminum alloy meets high-speed milling?
The Development of High-Speed Milling
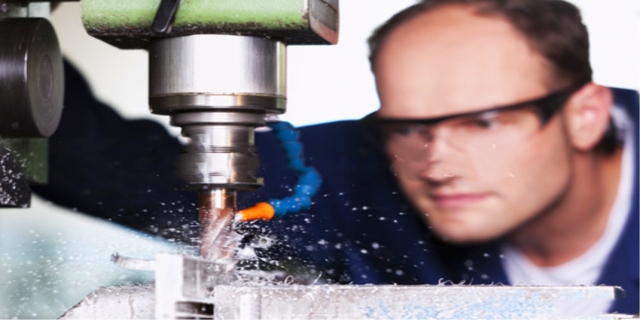
1. Conception Version | High-Speed Milling
In the 1990s, the development of high-speed milling (HSM) centered on the overall concept, which included the creation of machine tools with spindle speeds reaching 200,000 rpm. Both high spindle speeds and high feed rates were highly valued during this period. However, research institutes have shown that these high speeds can lead to serious consequences and significant risks when the tools or machine parts do not align properly with the application.
2. Optimization | Milling Application
The main factors to consider in high-speed milling are milling force, surface texture, metal removal rate, tool life, and safety. These studies underscore the importance of optimizing these factors to achieve the best results. Thanks to the research and development efforts of machine tool builders, software developers, and milling tool manufacturers, high-speed milling now has a broader application scope. More importantly, high-speed milling has moved beyond theoretical concepts and is actively applied in all aspects of the manufacturing process.
3. Innovation | Milling Tools
The development of innovative milling tools has made high-speed milling a more practical and profitable method in the mold manufacturing industry. Any rule in the milling process, including high-speed milling, impacts machine tools, software, and milling tools similarly. Over many years of practical applications, tool development in high-speed milling has evolved toward higher performance.
Milling is a crucial component of the high-speed milling process, and innovations in this area have significantly influenced the performance of milling cutters in various tooling applications. In high-speed milling, speed is paramount, encompassing spindle speed, milling speed, or feed rate. High-speed milling can be achieved by optimizing the milling process with high milling speeds or high feed rates.
New Development of Aluminum Milling
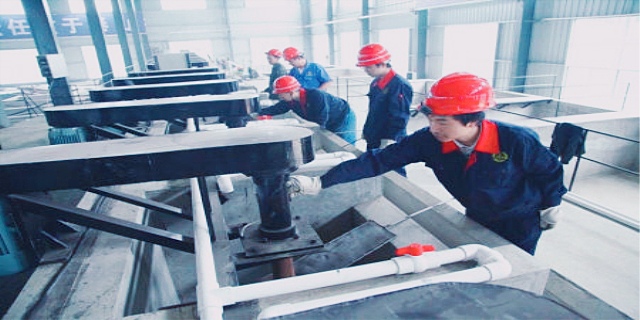
When it comes to high-speed milling and indexable inserts, ensuring the safe fixation of blades is paramount. The increasingly high spindle speeds and table feeds of milling machines, especially during aluminum milling, result in substantial centrifugal forces and significant loads on the blade mounting elements.
The finite element method (FEM) for analyzing load distribution is particularly valuable in developing effective solutions and identifying working models for indexable tools used in high-speed milling. FEM can also be used to design improved cooling systems, including liquid passages and outlet structures, to facilitate optimal chip evacuation. This has led to the creation of a new generation of high-speed milling tools for aluminum alloy milling.
The CoroMill 790 indexable end mill exemplifies a tool designed for machining aluminum alloys at high speeds. This type of end mill is primarily used in high-speed machining processes such as cavity milling, edge milling, slot milling, and contouring in mold manufacturing. The blade is securely fixed using a specially developed blade-knife interface. The design of the serrated contact surface on the bottom of the insert groove and the back of the blade not only significantly enhances safety in high-speed milling but also ensures processing accuracy.
The serrated contact surface design of the CoroMill 790 end mill can also be widely applied to face milling cutters used in aluminum machining, particularly for cast aluminum parts such as molds, engine blocks, and gearbox housings. From semi-finishing to super-finishing, when the milling speed is increased to 8000 m/min, the positive rake angle of the CoroMill 790 end mill can be made of cemented carbide, polycrystalline diamond (PCD), or cubic boron nitride (CBN). This design makes the milling cutter highly suitable for aluminum alloy milling and even cast iron milling. The high-tech structure of the CoroMill 790 end mill is not complicated; its blade axial adjustment is simple and convenient. It also offers the advantages of balanced milling forces, a wide application field, and precise machining allowances.
The blade is evenly stressed, resulting in smoother and safer processing, and extending the tool’s service life. This design greatly enhances milling quality and improves machining capacity.
Milled Aluminum in Automotive Manufacturing
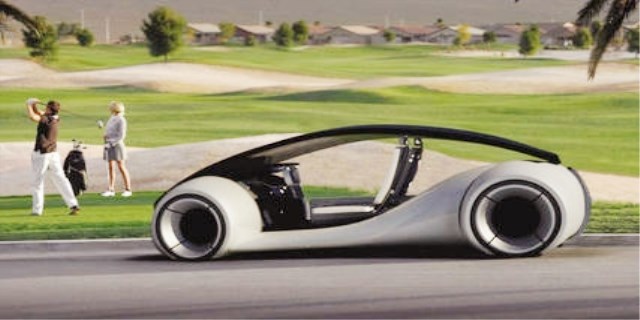
The use of aluminum alloy in automobile manufacturing is steadily increasing. For instance, the Jaguar long wheelbase version XF utilizes a significant amount of aluminum alloy. This vehicle claims that aside from the four doors, which are made of steel, the rest of the body comprises 75% aluminum alloy. So, which parts of the car can use aluminum?
Car Wheels
Firstly, car wheels. Modern car wheels are predominantly made of aluminum. If a car lacks aluminum wheels, it is either over a decade old or a very inexpensive model. Aluminum alloy wheels significantly reduce fuel consumption, and the most common material for these wheels is 6061 aluminum alloy (AL 6061).
Four Doors and Two Covers
Secondly, the “four doors and two covers.” These refer to the four doors, the hood, and the trunk lid. These parts of the car body are prone to damage. The aluminum alloy used for these components is 5182 aluminum (AL 5182). This alloy is chosen because of its excellent deformability, which allows it to absorb impact forces effectively, providing better protection for the driver and passengers. Therefore, for enhanced safety, the “four doors and two covers” are made of 5182 aluminum alloy.
Car Chassis
Additionally, the car chassis includes more aluminum components. The bottom plate of the suspension arm is made from aluminum alloys such as 5083, 5754, and 6061 aluminum.
Other Parts
Moreover, aluminum alloys are used in several other car components. These include the fuel tank, radiator, and the battery bottom plate in new energy vehicles.
Possibility of Milled Aluminum is Infinite
With the development of the metal industry, the current process of extracting metal materials from raw sources, processing them, and eventually recycling them ensures minimal waste of resources and reduced ecological impact. Aluminum alloy, in particular, stands out for its environmental friendliness and recyclability, aligning perfectly with contemporary environmental priorities. The milling process further enhances the versatility of aluminum, making it an integral part of various aspects of our daily lives.