Less than 50 years ago, the idea of automated production was a mere fantasy. Today, it’s as commonplace as a vending machine in an airport, thanks to the CNC prototyping service industry. While installing a robotic arm loader once required a specialist, many CNC machines now come with preset options that allow users to connect the arm themselves. However, automating CNC production should be carefully considered, as robots can be a significant investment.
When to Consider a Robot
Initially, CNC automation was reserved for repetitive tasks, highly precise operations, and hazardous environments. Now, with decreasing costs, the primary consideration for using robots is profitability. If the robot can increase your profits over the next five years more than it costs, it’s a worthwhile investment. Calculate your costs and potential profits, and if automation allows you to take on enough new work to cover a fifth of the robot’s cost annually, it’s time to invest.
Selecting the Right Robotic Arm
Robotic arms serve various purposes, from loading and unloading parts to performing welding and assembly tasks. For low-batch CNC production and prototype manufacturing, the most efficient choice is a robotic arm for loading and unloading parts.
Modern arms offer simplified programming. Previously, programming was complex and time-consuming, suitable only for large-scale production or high precision. Now, some arms feature learning modes, allowing you to manually guide them through tasks. The arm remembers these actions and replicates them, offering a quicker setup with adequate precision.
The Advantage of Loading Robotic Arms
The key advantage of a robotic arm is its ability to automate repetitive tasks. For identical part batches, the arm can handle production overnight, allowing you to simply load the blanks and return to a completed batch the next day. This capability effectively adds a second and third shift to your operations.
Setting Up and Integrating the Arm
Once you’ve decided to incorporate automation, ensure the robotic arm and CNC machine communicate effectively. They need to send and receive signals to coordinate their operations. For example, the arm should begin working once the CNC machine completes a task and opens its door.

Connecting the Arm to the Machine
The arm must receive a signal from the CNC machine to start loading a new part. It should also send a signal when it’s time for the CNC machine to clamp the part. If you’re familiar with mechatronics, you can connect the arm and machine through USB ports or equipment relays, using a conversion program to translate signals.
If you’re not a mechatronics expert, check the compatibility of the robotic arm with your CNC equipment. Consult the manufacturer for guidance, as they may provide manuals to assist with setup, saving you on technician costs.
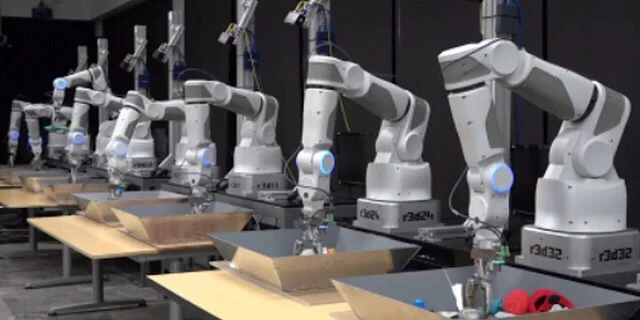
Programming the CNC Machine Door
Automated CNC production requires a machine tool with an automatic door. If your machine lacks this feature, consider purchasing one. Even with an automatic door, you might encounter issues, such as the door taking time to open. Program a delay for the arm to prevent collisions. If the control panel misinterprets the door’s delay as a jam, program the arm to manually press the “open/close door” button, mimicking a human operator.

How AS Prototypes Can Assist You
AS Prototypes specializes in rapid prototyping services and low-volume production, supporting the development of new automated CNC solutions. We have robust production capabilities and excellent supply chains, offering custom CNC machining and rapid injection molds with short lead times. If you’re interested in partnering with us for strategic support, please feel free to contact us.
