CNC milling is a precision machining process that transforms solid blocks of material into complex geometric shapes using computer-controlled milling machines and specialized cutting tools. The process involves a stationary workpiece and a rotating cutter, with the machine’s linear and rotary axes enabling intricate tool paths for high-accuracy results.
At AS Prototypes, we leverage advanced CNC milling technology to produce high-quality parts with tight tolerances. The tool paths are programmed using CAD/CAM software, allowing engineers to select from various milling operations tailored to specific part geometries.
Basic Types of Milling Operations
Different milling techniques achieve distinct geometric features. Below are some of the most common operations used in machining:
1. Plain Milling (Slab Milling)
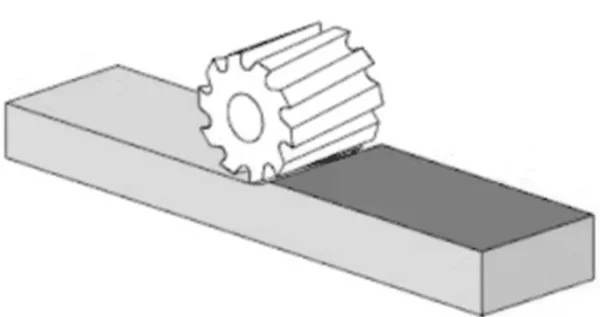
Plain milling uses a horizontal cutter to machine flat surfaces. The tool’s rotation aligns with the feed direction, making it ideal for roughing operations that convert raw material into precise prismatic shapes.
2. Face Milling
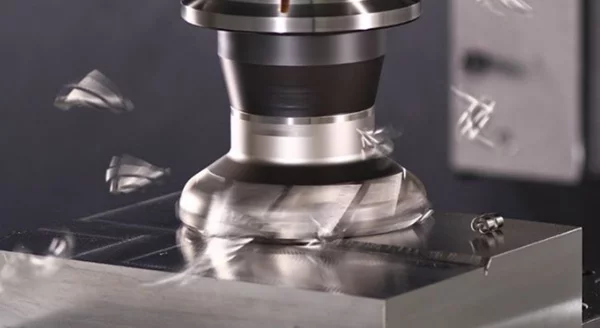
Unlike plain milling, face milling uses a cutter perpendicular to the workpiece, producing smooth, flat surfaces with excellent dimensional accuracy. This method is preferred for fine finishes and high parallelism.
3. Side Milling
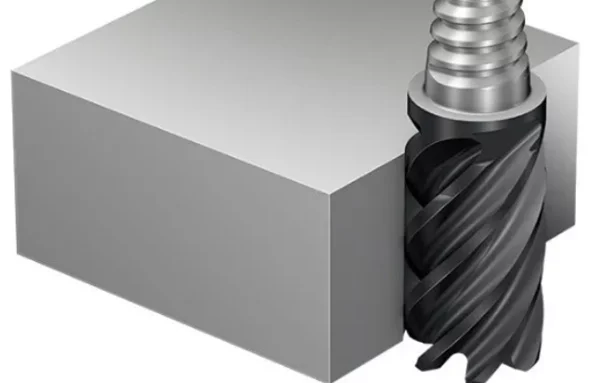
This process uses the cutter’s side edges to machine slots, profiles, or vertical walls. Care must be taken to avoid excessive cutting forces that could lead to tool deflection.
4. Shoulder Milling
Shoulder milling creates vertical walls and flat floors with sharp corners, often used in molds and dies where precise perpendicular shoulders are critical.
5. Angular Milling
Angular milling machines produce chamfers, grooves, or angled features using specialized cutters or fixtures. It’s commonly a finishing operation for aesthetic or functional edges.
6. Form Milling
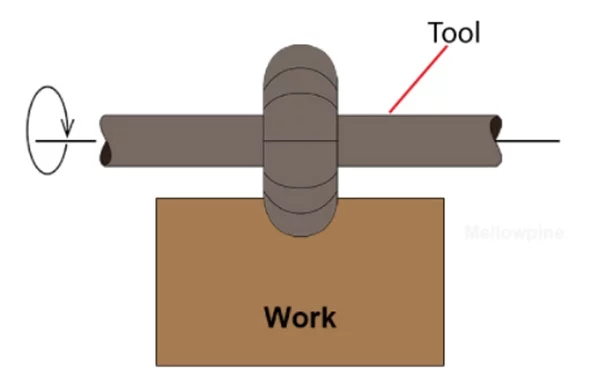
Form milling employs custom-shaped cutters to create complex contours like curves and arcs, frequently used in mold-making and tooling.
7. Profile Milling
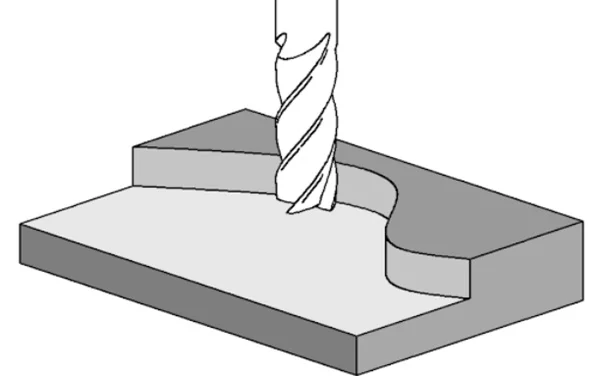
This advanced CNC operation produces intricate profiles with curves, arcs, and lines—essential for aerospace and automotive components.
8. Gang Milling
Multiple cutters on a single arbor machine different workpiece sections simultaneously, improving efficiency for parts requiring multiple cuts in the same orientation.
9. Gear Milling
Specialized cutters produce high-precision gears with complex tooth profiles.
10. Thread Milling
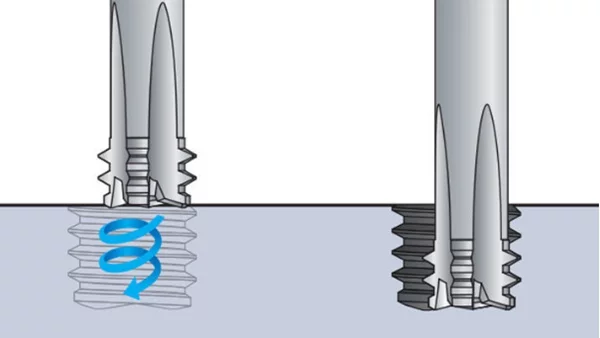
Thread milling cuts internal threads with helical toolpaths, offering flexibility in hole size, pitch, and thread profile compared to traditional tapping.
11. Slot Milling
Used for machining keyways, pockets, and grooves, slot milling employs T-slot cutters, end mills, or disc cutters depending on the slot geometry.
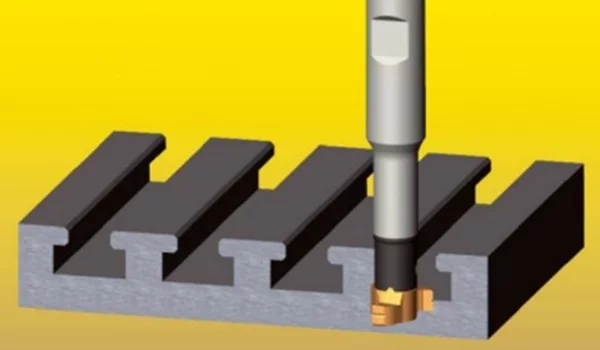
Advanced Milling Techniques
1. Multi-Axis CNC Milling
5-axis CNC milling (X, Y, Z + two rotary axes) enables machining of complex geometries like splines, undercuts, and freeform surfaces—crucial for aerospace, medical, and automotive industries.
2. Turn-Milling
A hybrid process combining turning and milling, turn-milling machines produce cylindrical and prismatic features in a single setup, enhancing productivity and accuracy.
3. Thin-Wall Milling
Special techniques like dynamic milling and adaptive feed rates prevent vibrations and deformations when machining delicate thin-walled parts like turbine blades.
Conventional vs. Climb Milling
- Conventional (Up Milling): The cutter opposes the feed direction, starting with a thin chip and increasing thickness. More stable but less efficient.
- Climb (Down Milling): The cutter moves with the feed, starting with a thick chip that tapers off. Offers better tool life and surface finish.
Choosing the Right Milling Process
Key factors include:
- Part Geometry (e.g., curves, threads, slots)
- Machine Capability (3-axis vs. 5-axis CNC)
- Quality Requirements (tolerances, surface finish)
Cutting Parameters in Milling
- Feed Rate (mm/min, mm/tooth) – Affects productivity and surface quality.
- Cutting Speed (RPM) – Impacts tool wear and heat generation.
- Depth of Cut (Radial & Axial) – Influences cutting forces and material removal rate.
Precision CNC Milling at AS Prototypes
At AS Prototypes, we specialize in high-tolerance CNC milling using 3-, 4-, and 5-axis machining centers. Our expertise spans metals and plastics, delivering rapid prototyping and low-volume production with exceptional surface finishes for industries like automotive, aerospace, and medical devices.
📩 Contact us today at info@asprototypes.com for your CNC milling needs!
FAQs
Q: How is CNC milling different from conventional milling?
A: CNC milling is fully automated via computer control, ensuring higher precision and repeatability compared to manual operation.
Q: Is milling suitable for volume production?
A: Yes, CNC milling is widely used in mass production due to its speed and consistency.
Q: How do I select the right milling operation?
A: Consider part geometry, quality requirements, and machine capabilities—our team at AS Prototypes can help optimize your process.