Counterbore and spotface operations are among the most frequently used hole-making techniques in machining. Although both are designed to accommodate fastener heads, their subtle differences often lead to confusion among professionals.
This article provides an in-depth comparison of counterbore and spotface holes. Continue reading to learn more!
What Is A Counterbore Hole?
Let’s start with a straightforward question: What is a counterbore hole? A counterbore hole is a flat, cylindrical recess machined coaxially around an existing screw or fastener hole.
The primary purpose of a counterbore is to provide a convenient, non-intrusive space for the fastener’s head. This recess is deep enough to allow the fastener head to sit flush with or below the surface of the workpiece.
This design feature is often essential in many parts, where protruding fastener heads are undesirable due to assembly constraints or aesthetic considerations.
For instance, consider the image below. The screw is necessary to assemble the electrical socket components. However, the screw head could obstruct plugs from fully connecting to the socket. To address this issue, a counterbore hole is added.
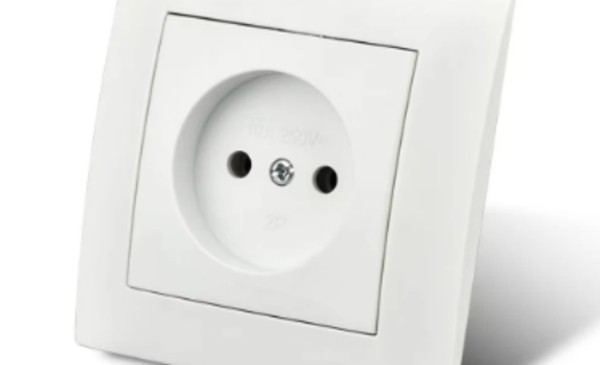
Counterbores In Engineering Drawings
Holemaking is a diverse machining operation that encompasses various hole geometries. Due to the variety of holes in engineering design, a counterbored hole is typically specified on a drawing using a counterbore callout.
An example can be seen in the figure below. The technical drawing illustrates a 13.5-diameter drill hole with a counterbore. This drill hole will act as the pilot hole for the counterbore operation.
The counterbore callout specifies the size of the counterbore as 23.79 and its depth as 7.5.
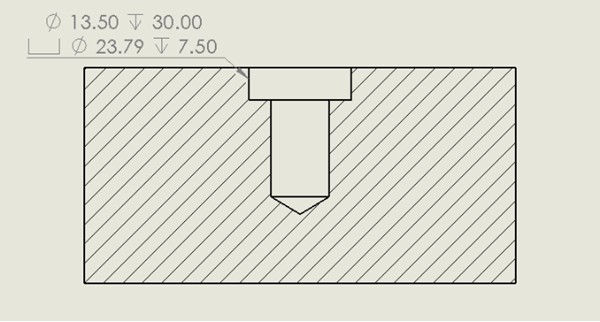
What Is a Spotface Hole?
To continue our discussion on spotface vs counterbore, let’s explore what a spotface is. Simply put, a spotface is a shallow counterbore. Like a counterbore, it is a flat, cylindrical recess over a pilot hole, but the depth of a spotface hole is much shallower than that of a conventional counterbore.
Functions of Spotface Holes
The primary function of a spotface is to provide fasteners with a flat, level seat to sit against. An uneven or rough fastener seat can create unwanted stresses in the fastener’s body, potentially causing damage. Therefore, a spotface ensures a smooth mounting surface for the fastener head.
Another significant application of a spotface hole is to facilitate fastener installation at an angle. Some assemblies require fasteners to be positioned at an angle to a flat surface, necessitating a flat seat for proper fastener assembly. This flat seat is achieved with a spotface, as illustrated in the figure below.
It’s important to note that a spotface should not be confused with a countersink. While similar, countersinks have an angled bottom to accommodate cone-shaped screw heads, unlike the flat bottom of a spotface hole.
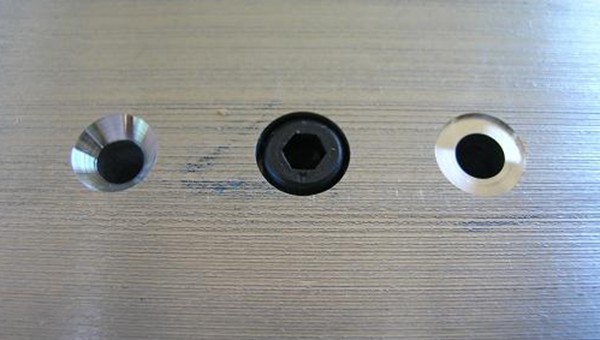
Spotface Holes in Engineering Drawings
Similar to counterbores, spotface holes are represented by a unique symbol in engineering drawings. The spotface symbol is based on the counterbore callout but includes an ‘SF’ marking inside the standard counterbore symbol, indicating a Spot Face.
The image below provides a straightforward example of a spotface callout. In this instance, the spotface feature has a diameter of 50 and a depth of 1.
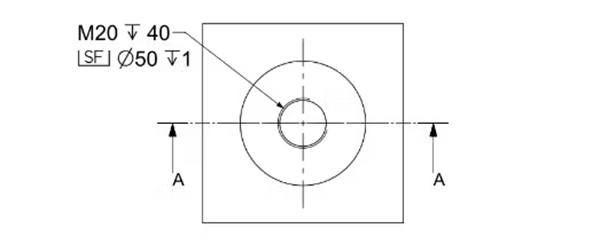
Counterbore Vs Spotface: A Detailed Comparison
Now that we have a clear understanding of both counterbore and spotface holes, it’s time to delve deeper into the comparison between the two. Although they are quite similar, their unique characteristics become evident when you explore their differences.
The following discussion highlights the major differences between spotface and counterbore holes.
Function
The primary distinction between counterbores and spotfaces lies in their design applications. However, before diving into their differences, it’s important to note their common purpose: both counterbores and spotfaces provide a flat seat and recess for fastener heads.
Counterbores, in particular, are designed to completely enclose the fastener head beneath the workpiece surface. This prevents the fastener head from protruding above the surface, thereby avoiding assembly restrictions.
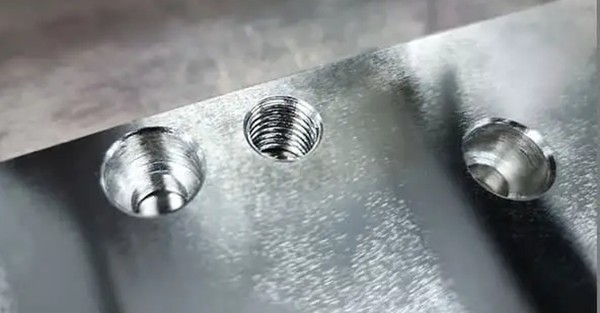
Depth
Counterbores and spotfaces differ significantly in terms of hole depth. As explained earlier, counterbores are designed to be at least as deep as the height of the fastener head, ensuring that the fastener head is completely concealed beneath the surface after assembly.
In contrast, spotface depth is much shallower. It is just deep enough to provide a flat, recessed seat for the fastener head.
Engineering Drawing Symbol
Another major difference between spotface and counterbore holes lies in their engineering drawing callouts. As previously discussed, the counterbore callout includes the ‘⌴’ symbol, representing the cross-section of a counterbore, along with the diameter and depth specifications.
The spotface symbol is derived from the counterbore symbol but includes an ‘SF’ inside it. This notation conveys the designer’s intent to the machine operator, specifying the exact diameter, depth, and surface finish required.
Surface Finish
The surface finish is another key difference in the comparison between counterbores and spotfaces. Both types of holes are kept smooth to ensure a flat, even mounting surface for fasteners. However, spotfaces typically have a finer surface finish.
This is because the primary purpose of a spotface is to provide a level mounting surface to achieve the correct clamping pressure. In contrast, counterbores can have rough side walls without compromising their functionality.
A Brief Table
Counterbore | Spotface | |
Functions | Provide a cylindrical recess to fastener heads to sit flush against a surface. | Provide a smooth seat for fastener heads to sit against. |
Depth | At least as deep as the fastener head’s height to completely conceal it. | Very shallow depths, typically less than 5 mm. |
Size | Diameter and depth are both equally important in defining counterbore size. | The main dimension of a spotface hole is the diameter, with the depth being a secondary dimension with loose tolerance. |
Symbol | ⌴ | SF |
Counterbore And Spotface Machining
Machining counterbore and spotface holes is generally straightforward, but the machinist must follow the correct procedure. Both types of holes require an initial pilot hole, which can be created using standard hole-making techniques such as drilling, boring, or milling.
The next step involves using specialized counterbore or spotface tools of the appropriate size to achieve the desired hole dimensions.
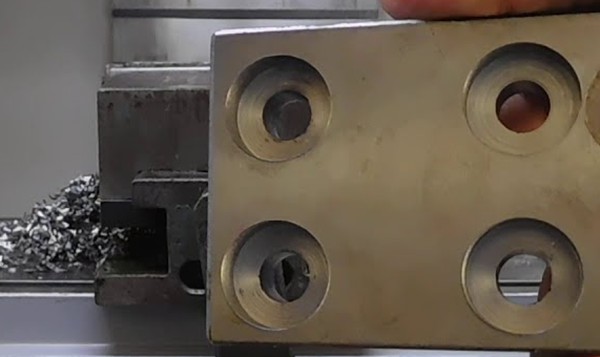
For this process, the most crucial objective is to ensure that the tool is perfectly coaxial with the pilot hole. Any misalignment can violate the tolerance on the hole dimensions, potentially preventing the fastener from fitting properly into the counterbore or spotface.
The final step in the machining operation involves enlarging the pilot hole to create the desired feature. Since counterbores and spotface holes are typically secondary geometric features, experts often choose between manual machining and CNC machining based on the primary part geometry.
Whatever the chosen method, it also applies to auxiliary hole-making procedures like counterbore and spotface machining.
Counterbore And Spotface Tools
An important distinction in the spotface vs. counterbore discussion is the difference in the machining tools used for each feature. While there isn’t a dedicated tool for each, as both share similar geometries, machinists sometimes employ specialized tools for these operations.
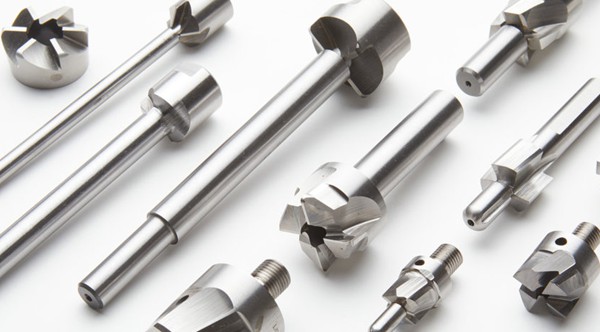
The image below illustrates these different geometries. A counterbore tool resembles a milling tool or a reamer because it needs to achieve a greater depth. In contrast, a spotface tool typically has very short cutting teeth.
Additionally, some of these tools feature a central anchor to guide the tool within the pilot hole, ensuring coaxial alignment and straight descent along the toolpath.
Conclusion
The features of counterbore and spotface holes play a crucial role in manufacturing complex assemblies and are essential for ensuring the success of a design. As engineers or manufacturers, understanding their differences, engineering drawing symbols, and machining techniques and tools is invaluable.
AS Prototypes is a custom manufacturing company specializing in CNC machining services. Our dedicated team is highly experienced in providing manufacturing solutions for custom machined parts, including counterbore and spotface components.
Contact us with your projects and receive an instant quote!
FAQs
Are counterbore and spotface machined with different tools?
Yes, there are specialized tools for both operations. However, in some cases, they can also be machined with similar tools like endmills or finished with a reamer.
What is the main difference between counterbore and spotface?
A counterbore is typically deeper than a spotface. The primary purpose of a counterbore is to provide a level seat for the fastener and to fully encompass the fastener head. In contrast, a spotface is machined solely to provide a balanced, level seat for the fastener.
How are spotfaces and counterbores dimensioned?
Counterbores are dimensioned based on the size of the fastener head. The diameter should be large enough to accommodate the fastener head, and the depth must be at least as great as the height of the fastener head to ensure it is fully recessed within the workpiece surface.
For spotfaces, the diameter dimensioning is similar to that of counterbores, but the hole depth is determined by the designer. Typically, the depth is kept very shallow, usually under 0.5 mm.