Flanges are crucial elements in many mechanical systems. They provide a mechanical method for connecting or assembling components like pipes, fittings, and valves. Additionally, flanges are designed to be disassembled, making them perfect for systems that require regular maintenance.
But what exactly is a flange? What types of flanges are there? What factors should be considered when designing flanges? Keep reading as we provide the information you need to make informed manufacturing decisions.
What Is A Flange?
Flanges, which are rim-like, symmetrical disc components, are used to connect or seal pipes, containers, or fixed-shaft mechanical parts. These disc-shaped elements are commonly found in plumbing and are typically used in pairs. Various fasteners, including threaded fixings, are employed to secure the flanges in place.
Additionally, flanges are designed with bolt holes. Typically, two flanges are attached to the ends of pipes with a gasket in between, and bolts are used to create a secure connection between them.
Characteristics Of Flanges
- Flanges have accurately drilled holes for easy assembly.
- They have controlled grain flow for optimal strength and stiffness.
- To facilitate good welding, flanges are machined bevels.
- For unrestricted flow when used for piping system, flanges are smooth and have accurate bore.
- This component has spot-facing to ensure fastener seating stays true and square.
How Does Flange Connection Work?
A flange connection consists of assembling two pieces of equipment, pipes, or pipe fittings with two flanges, flange mats, and bolts. Various types of washers are also used to secure the flange connection.
Additionally, a flange connection joins two materials using inner and outer lip parts, or flanges. To create a seal between the opposing flange faces, force (either gasket compression or sealing pressure) must be applied and maintained. To ensure the flanges remain in place, they are typically bolted together with a gasket between the faces, forming a tight seal. One common type of gasket used for this purpose is a disk spring, which is a specific type of spring.
Common Types Of Flanges And Their Uses
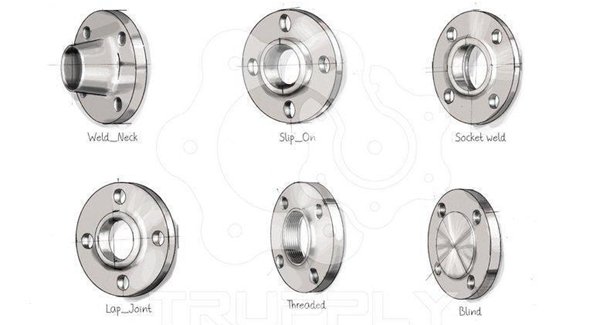
Selecting the appropriate flange for your piping system or intended joining application ensures reliable performance, longevity, and cost-effectiveness. Here are some common types of flanges and their uses.
Socket-Weld Flanges
Socket-weld flanges feature a connection where the pipe is inserted into the flange, similar to snap-fit joints. A multi-pass fillet weld secures the connection, making socket-weld flanges ideal for smaller pipe diameters in low-temperature and low-pressure conditions. These flanges eliminate the limitations of threaded ends and are easier to install compared to other welded flanges.
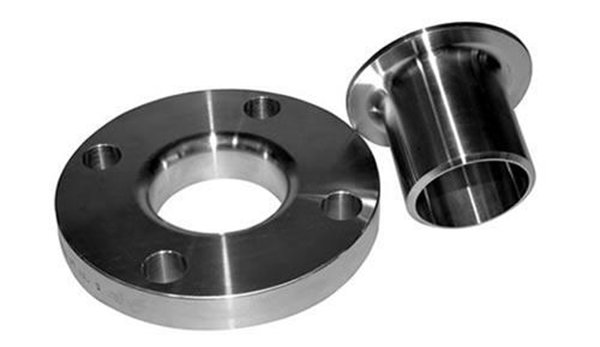
Lap Joint Flanges
Lap flange joints have a two-piece construction, and the flanged connection is made by welding the shaft end to the pipe or fitting and using a backing flange. Because of its design, this form is well-liked for usage in systems with constrained dimensions or requiring frequent disassembly and maintenance.
Blind Flanges
Blind flanges, simply blank discs that are easy to bolt, find use in the isolation or termination of piping systems. When placed correctly and used with the appropriate gaskets, they can create an excellent seal that is simple to remove when necessary.
Weld Neck Flanges
Weld neck flanges need to be shaft welded to be installed, just like lap flange joints. However, their reliability makes them a popular option for process pipes. They also perform excellently in systems with several repeat bends, making them ideal for high-temperature and pressure systems.
Slip-On Flanges
Slip-on flanges are widely used and come in various sizes to support systems with increased flow rates and throughout. All you need to do is match the pipe’s outer diameter to the flange. The flange must be securely fastened to the pipe on both sides, which makes installation a little more technical.
Threaded Flanges
This design, also called a flange screw, features a thread inside the flange bore that matches the male thread on the pipe or fitting. You may dispense with welding in many applications thanks to the threaded connection. To use threaded flanges, matching the thread to the pipes you want to connect is best.
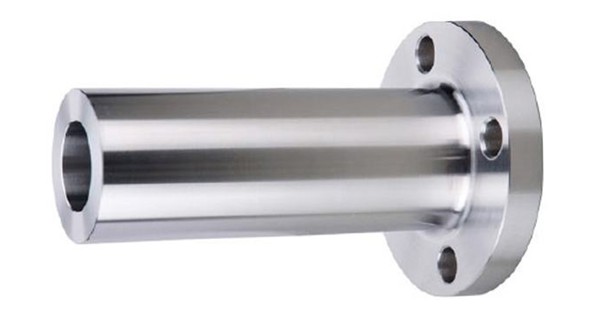
Long Neck Welding Flanges
Long weld neck flanges, also known as integral flanges, indicate that the neck of a welding neck flange is extremely lengthy. The welding neck flange commonly features a conical neck and a bevel end butted together with the complementary pipe.
Orifice Flanges
When orifice plates or flow nozzles are utilized, orifice flanges are used instead of the typical pipe flanges. This mainly aims to gauge how quickly gases or liquids are moving through the appropriate pipeline.
Special Flange Types You Need to Know
Special flanges are flange types that are suitable for use in a diverse range of environments. They also include flange types with a diverse range of uses. Special flange types include:
- Expanding flanges
- Nipo Flanges
- Reducing flanges
- High hub flanges
- Ring type flanges
- Groove and tongue flanges
- Loose flanges
- Spectacle blind flanges
Different Face Of A Flange To Connect
Face type is an important concept to consider when choosing flanges. The reason is that the type of face a flange has determines the type of gasket needed to install it and the type of seal it would create.
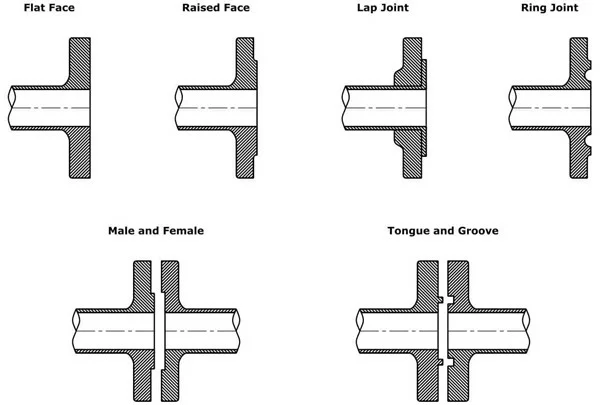
Below are the different faces of a flange.
Raised Face (RF): These flanges feature an inner bore circle gasket and a small elevated section around the bore. Raised face flanges are available for various pressure and temperature ratings and are the most commonly used flange in the oil and gas and chemical engineering industries.
Male and Female Face (M&F): These flanges have raised sections and corresponding grooves to hold the gasket in place. The gasket retention occurs on the female face, allowing for more precise positioning and compatibility with a wider range of materials.
Tongue and Groove (T&G): These flanges have grooves and raised areas similar to male and female face flanges. This design facilitates installation by promoting self-alignment of the flanges and creating a reservoir for gasket adhesive.
Flat Face: As the name suggests, flat face flanges have a smooth, flat surface. They use a full-face gasket that covers most of the flange surface.
Ring Joint Face (RTJ): This type of flange is used in high-pressure and high-temperature applications. It features a notch where a metal gasket is placed to maintain the seal.
Flange Dimensions And Considerations For Ensuring The Right Sizes
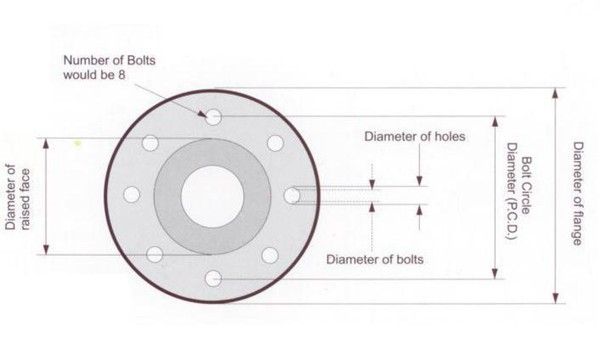
Flanges are most likely influenced by flange size when developing, maintaining, or enhancing a piping system. To ensure the flange is sized correctly, you must consider how it connects to the pipe and the gaskets being used. Here are some considerations when choosing flange dimensions.
- Thickness: When choosing a flange, it is best to consider thickness—the thickness of the outer attaching rim.
- Normal bore size: This measures the inner diameter of the flange connectors
- Bolt circle diameter: When measured from center to center, this is the distance between bolt holes on opposite sides.
- Pipe size: A pipe size ideal for the flange being used.
Below are tables showing flange dimensions.
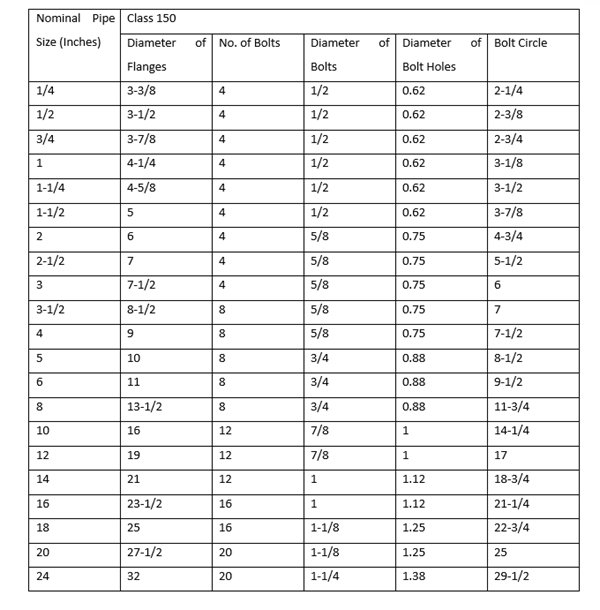
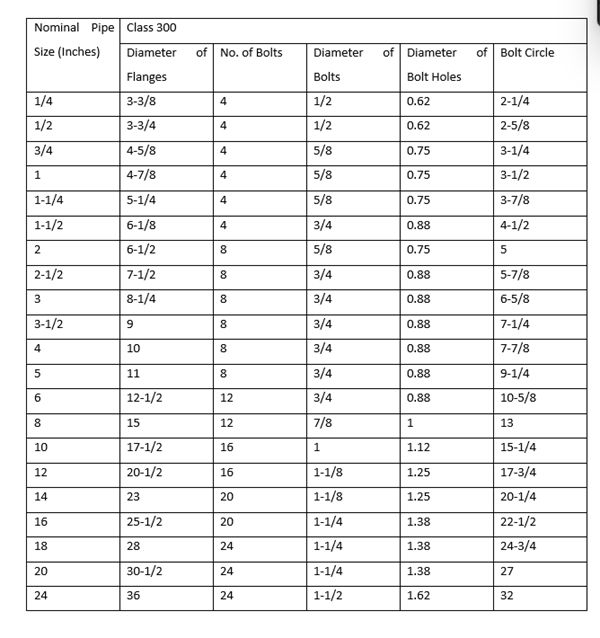
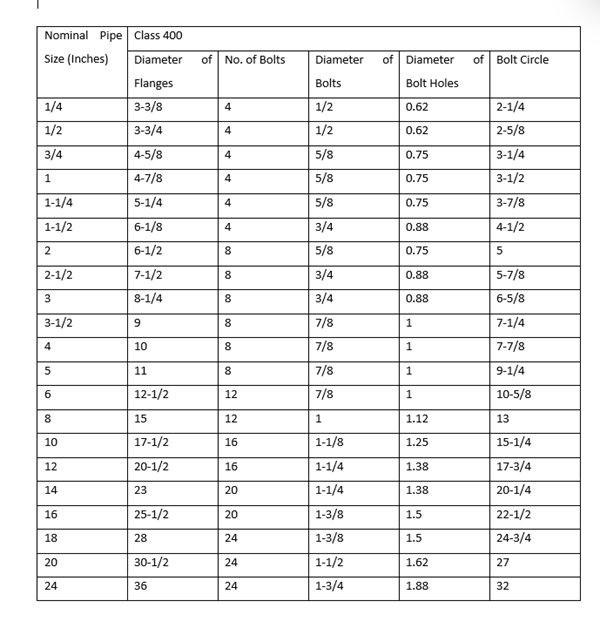
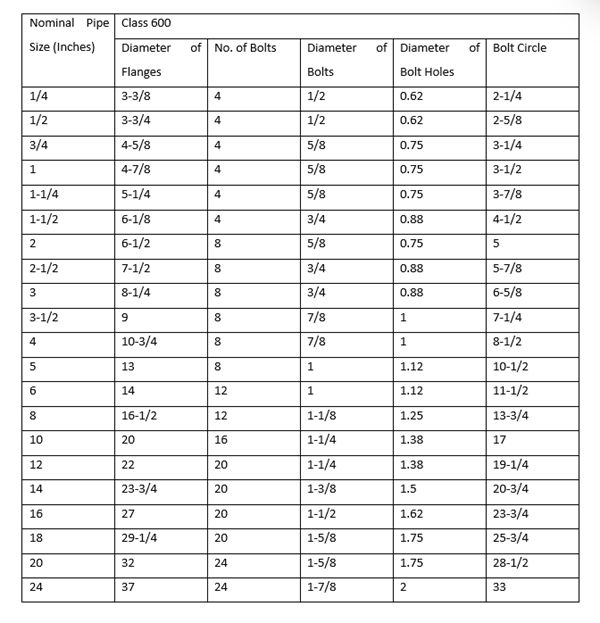
Flange Standards And Markings
Flange designs are governed by the international standards ASME B16.5 & B16.47, which facilitate comparison. These standards were developed by the American Society of Mechanical Engineers (ASME).
All flanges must have markers to aid in replacing or verifying existing parts. Typically, these markers are located on the outer perimeter of the flange.
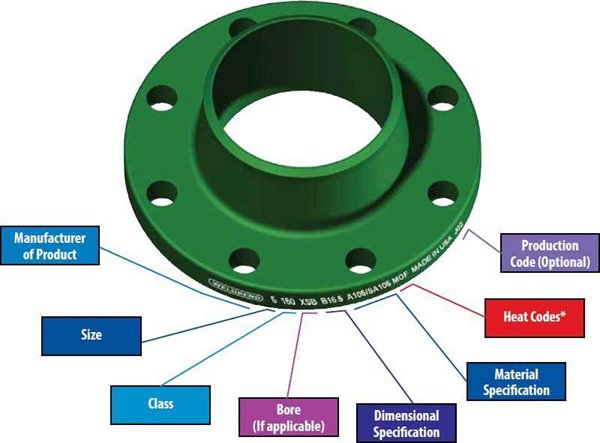
These indicators also adhere to a rigid hierarchy:
- Logo or code for the manufacturer
- ASTM code of materials
- Material quality
- Pressure-temperature class service rating
- Size
- The thickness (Timeline)
- Heat index
- Bore
- Any special identifiers, such as QT for quenched and tempered or W for welding repair
Machining Process Of Flange Parts
Several stages are involved in the flange part machining process, ranging from material selection to surface finish. Below is the machining process for making high-quality flanges.
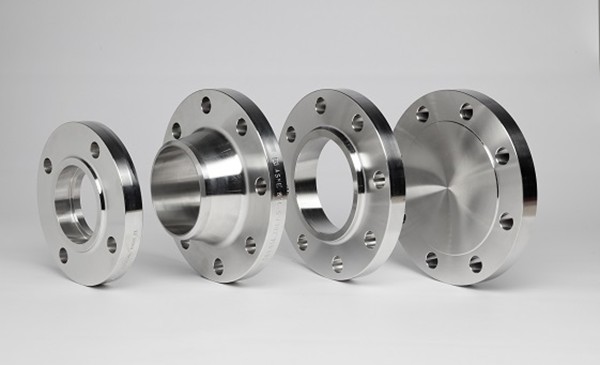
Material Selection
Picking the right flange materials is the first stage in the machining process. The most popular materials for making flanges are alloy steel, carbon steel, or stainless steel. However, the ideal material often depends on the application’s temperature, pressure, and corrosion resistance needs.
Material Cutting and Shaping
Following selection, the material is sliced and formed. Big metal plates are cut into smaller pieces to get the right size for the flange. The produced parts are then heated to the proper temperature to prepare them for further processing.
Heat Treatment
Depending on the material and purpose of a flange, the flanges may undergo heat treatment methods such as annealing, quenching, or tempering. Heat treatment boosts the flange’s mechanical properties while enhancing its resilience, toughness, and resistance to wear and corrosion.
Forming and Forging
The heating process makes the metal components malleable, facilitating the proper flange shape development. Machinists utilize different methods to forge the flange, including hot forging and cold forging. The metal is formed at room temperature in cold forging, while hot forging involves forming heated material/metal under high pressure.
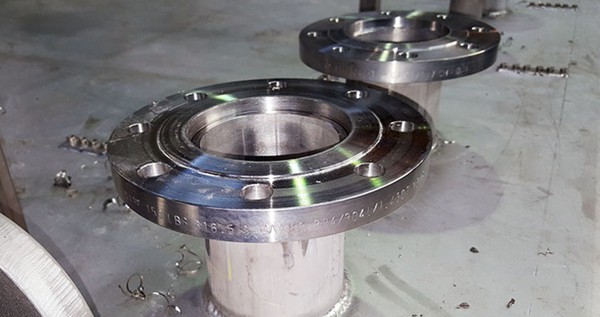
Machining
After the initial cutting and shaping, the flange is machined to achieve precise tolerances and to refine its dimensions. This operation includes facing sealing surfaces, chamfering edges, and drilling holes for bolt connections. CNC (Computer Numerical Control) machines are often used for automated and precision machining.
Surface Finish
Flanges might undergo surface finishing operations like grinding or polishing to achieve the desired smoothness, remove surface defects, and improve their overall look.
Inspection and Quality Control
Quality control is an important stage in the production of flanges. Flanges undergo a thorough examination process to ensure they comply with the appropriate norms and specifications. Inspecting for quality control includes measurement inspections, finishes and surface analyses, and non-destructive testing methods like ultrasound or magnetic particle analysis.
Conclusion
Manufacturing or machining flanges involves several processes to ensure the highest quality. There are also standards that govern their production and markings that aid in verification for replacement or manufacturing. Additionally, various types of flanges exist, each with specific and unique applications.
AS Prototypes is a professional manufacturing company specializing in machining prototypes and parts, including flanges and other fastener components. We uphold high standards to deliver high-quality machining services to numerous sectors at affordable costs. Our team of engineers is always ready to receive your orders and process them promptly, reducing time to market.
FAQs
What materials are ideal for making flanges?
Flanges are commonly made from materials such as carbon steel, cast iron, nickel alloy, stainless steel, bronze, brass, and aluminum.
What are the specifications of flanges?
Standard flanges are governed by the ASME B16.5 and ASME B16.47 specifications, while European steel flanges adhere to the EN 1092-1 specification.
When is it best to use a flange fitting?
Flange fittings are ideal for high-pressure situations where larger connections simplify assembly compared to using numerous large fittings. They also feature a zero-clearance design, making it easy to disconnect and reconnect them for maintaining manifold, tube, and hose connections.