Mold manufacturing technology has advanced rapidly, becoming a crucial component of modern manufacturing. This includes mold CAD/CAM technology, laser rapid prototyping, precision prototyping, ultra-precision machining, and the use of finite element and boundary element methods for dynamic simulation of flow, cooling, and heat transfer processes. Additionally, mold CIMS technology, DNM technology, and CNC technology have been developed, encompassing nearly all aspects of modern manufacturing technology.
The current trend in mold manufacturing technology is towards accelerating information-driven processes, enhancing manufacturing flexibility, increasing agility, and achieving systematized integration.
1. The 3rd Generation Of Mold Technology | High-Speed Milling
The high-speed milling process offers not only high speed and excellent machining accuracy and surface quality, but also operates at a low temperature (with workpiece temperature increasing by only 3°C), resulting in minimal thermal deformation compared to traditional cutting methods. This makes it suitable for processing temperature-sensitive materials like magnesium alloy. Additionally, due to the small cutting forces involved, it is ideal for machining thin-walled and rigid parts. By selecting appropriate tools and cutting parameters, high-speed milling can also handle hard materials (up to HRC60). Consequently, high-speed milling technology remains a hot topic, advancing towards greater agility, intelligence, and integration, and is recognized as the third-generation modeling technology.
2. Electric Discharge Milling & “GREEN” Product Technology
From an international perspective, Electric Discharge Milling (EDM) technology has achieved high levels of performance, process indicators, intelligence, and automation. The current trend in EDM technology research and development is focused on EDM Milling Technology, which serves as an alternative to traditional cavity-forming electrode processing. This innovative approach uses the high-speed rotation of simple tubular electrodes for three-dimensional or two-dimensional contouring, similar to CNC milling. This advancement represents a significant development in the EDM field, eliminating the need to create complex forming electrodes.

With the progress of EDM technology, increasing attention is being paid to the safety protection technology of EDM machines. Many electric machines now incorporate advanced security protection features. Currently, the European Commission (EC) mandates that machines without the “CE” mark cannot enter the EC market. Similarly, the international market is increasingly emphasizing safety protection technical requirements.
Additionally, there is a growing focus on “green” products in the international market. As a dominant mold processing equipment, EDM machine tools must address environmental concerns and develop sustainable solutions for the future.
3. New Generation Of Mold CAD/CAM Software Technology
The mold software currently developed by countries such as the UK, USA, and Germany, as well as by some universities and research institutes, exhibits characteristics of intelligence, integration, and mold manufacturability evaluation. This represents a new generation of mold CAD/CAM software.
This new generation of mold software is grounded in the practical experiences of mold design. The knowledge has been systematically and scientifically organized to create an engineering knowledge base that can be easily accessed by the mold. With the support of intelligent software, mold CAD transcends traditional design and calculation methods. Instead, guided by advanced design theories, it leverages expert knowledge and successful industry experiences to produce designs that are both reasonable and advanced.
The new generation of mold software designs mold structures using stereoscopic thinking and intuitive perception. The generated three-dimensional structure information can be seamlessly used for CNC machining evaluations, requiring three-dimensional parametric feature modeling, molding process simulation, numerical control machining process simulation, and comprehensive information exchange and management. This high level of integration ensures that functional modules are not only complete but also share a unified data model, forming a cohesive global dynamic database. This facilitates integrated management and information sharing throughout the entire process of mold design, manufacturing, assembly, testing, and commissioning.
The manufacturability evaluation function is crucial in the new generation of mold software. It should filter multiple programs, assess the rationality and cost-effectiveness of the mold design process, and provide modification suggestions for die designers.
Manufacturability evaluation encompasses mold design and manufacturing cost estimates, mold assembly evaluation, mold parts manufacturing process evaluation, and mold structure and forming performance evaluation. The new software should also feature assembly-oriented functions, as the mold’s functionality is realized through its assembly structure. By adopting an assembly-oriented design approach, mold assembly is no longer just a simple aggregation of parts. The data structure can describe the mold’s function and define the relationships between parts and components, thereby ensuring the mold’s quality effectively.
4. Advanced Manufacturing Technology | Rapid Tooling
With the rapid development of Laser Rapid Prototyping (RPM), China has reached an international level and is gradually commercializing these technologies. The main commercialized rapid prototyping processes worldwide include SLA (stereolithography), LOM (layered object manufacturing), SLS (selective laser sintering), and 3D-P (3D printing).
Tsinghua University was the first to introduce the SLA250 (stereolithography or photosensitive resin laser curing) equipment and technology from the American 3D company, initiating research and development in this field. After years of dedicated effort and numerous improvements, they launched the “M-RPMS – Multi-functional Rapid Prototyping Manufacturing System” (which includes LOM-SSM and melt extrusion – MEM). This system is unique in the world, featuring two rapid prototyping processes and backed by China’s independent intellectual property rights (national patent), offering superior cost performance.
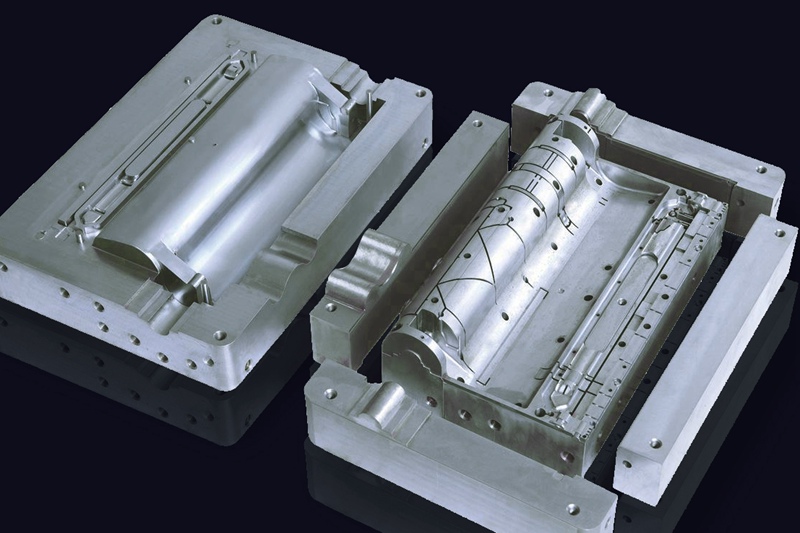
No-mold multi-point forming technology is another advanced manufacturing approach that uses a highly adjustable punch group instead of traditional molds. This technology enables the rapid and economical automatic forming of 3D surfaces, primarily through the use of CAD/CAM/CAT technology in the moldless multi-point forming system. Jilin Industrial University has undertaken a national key scientific and technological project on moldless forming and has autonomously designed and manufactured world-leading moldless multi-point forming equipment.
Compared with institutions such as the Massachusetts Institute of Technology (MIT), Tokyo University, and the Tokyo Institute of Technology, China’s technology is at the forefront in the practical application of theoretical research and is currently being promoted for wider adoption and application.
The resin stamping mold has been successfully applied for the first time in the trial production of domestic cars. FAW Mold Manufacturing Co., Ltd. designed and manufactured 12 sets of resin molds for a new car prototype trial. These molds include parts such as luggage compartments, hoods, and front and rear fenders, which are large and complex internal and external cover drawings. The main features of these molds are:
- The mold surface is based on CAD/CAM processing of the main model.
- High-strength resin casting is used, employing Swiss Ciba technology.
- The clearance between the convex and concave dies is controlled by imported special wax sheets.
- The molds exhibit high dimensional accuracy.
- The manufacturing cycle can be reduced by 50% to 67%.
- Manufacturing costs can be saved by 10 million yuan for the 12 sets of molds.
This development has opened up new possibilities for the trial production of small cars and marks a pioneering achievement in China. Swiss Ciba experts believe that these molds meet international standards as of the 1990s.
5. Field-Based Mold Testing Technology
With the advancement of precision mold technology, the requirements for measurement accuracy have become increasingly stringent. Traditionally, precision three-coordinate measuring machines have been limited by environmental conditions and were rarely used directly on the production floor. However, the new generation of three-coordinate measuring machines has been designed with features such as temperature compensation, anti-vibration materials, and dust-proof measures. These enhancements improve their environmental adaptability and reliability, enabling easy installation in workshops and facilitating on-site measurement.
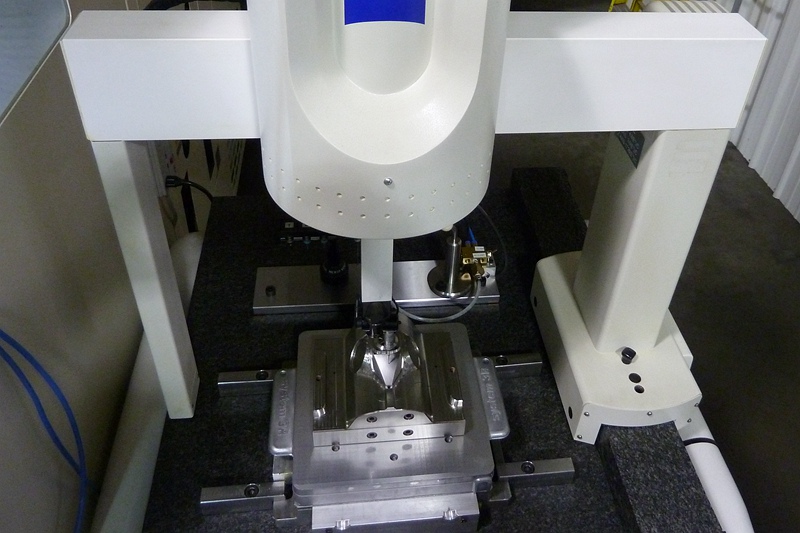
6. Mold Surface Engineering Technology Of Mirror Polishing
Mold polishing technology is not only a crucial aspect of mold surface engineering but also an essential process in mold manufacturing.
Currently, domestic polishing tools and abrasives can achieve a surface roughness of Ra0.05μm, which generally meets industry needs. However, achieving mirror polishing with a surface roughness of Ra0.025μm remains in the exploratory stage, with equipment, abrasives, and processes still under development.
With the large-scale application of mirror injection molds in production, mold polishing technology has become a critical issue. Due to ongoing challenges in polishing technology and materials within China—such as for optical lenses, injection molds, and high-transparency products like CDs and VCDs—a significant portion of high-precision injection molds still relies on imports.
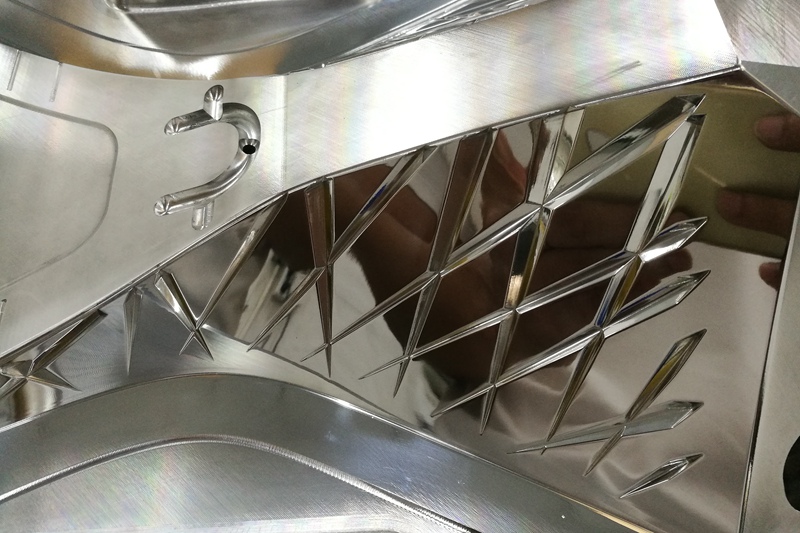
It is worth noting that the polishing of mold surfaces is influenced not only by the polishing equipment and technology but also by the inherent properties of the mold material itself, which has not yet received sufficient attention. In other words, the effectiveness of polishing is constrained by the quality of the mold materials. For instance, using 45# carbon steel for molds can achieve a surface roughness of Ra0.2μm, but visible defects may still be present. Further polishing can only enhance brightness without improving roughness. Consequently, imported mold materials are often used in domestic mirror mold production, such as Sweden’s ASSAB 136 and Japan’s Datong PD555, which can achieve satisfactory mirror finishes.
The suitability of mirror mold materials is not solely determined by their chemical composition. More importantly, it involves advanced manufacturing processes such as vacuum degassing during smelting, argon protection during ingot casting, vertical continuous casting and rolling, and soft forging. These processes result in mirror mold steel with fewer internal defects and impurities, fine grain size, high degree of dispersion, and good uniformity. These qualities are essential to meet the stringent requirements for mirror-polished steel.
Conclusion
AS Prototypes has positioned itself at the forefront of the global manufacturing industry through the development of advanced mold technologies, including Laser Rapid Prototyping (RPM) and no-mold multi-point forming. Innovations from leading institutions such as Tsinghua University and Jilin Industrial University have significantly enhanced our precision and efficiency. Our high-performance resin stamping molds and advancements in mold polishing technology further demonstrate AS Prototypes’ capability to produce high-quality molds.
However, achieving ultra-fine surface roughness and mirror polishing remains a challenge. The limitations of domestic materials and the need for advanced manufacturing processes highlight the importance of ongoing research and development. To meet the stringent requirements of mirror-finished molds, we rely on high-quality imported materials, such as Sweden’s ASSAB 136 and Japan’s Datong PD555.
The integration of intelligent software, advanced manufacturing techniques, and high-quality materials is crucial for the continued progress of AS Prototypes. By addressing current challenges and leveraging technological innovations, AS Prototypes is well-positioned to maintain its competitive edge and achieve further breakthroughs in mold technology.