Electronic Appliance Prototyping And Manufacturing
Prototyping and rapid manufacturing are essential components of the electronic appliance design and development cycle. These techniques allow you to quickly produce prototype and low-volume production parts for lab testing, user trials, and ultimately, market introduction, accelerating the entire process from initial concept to market entry.
The Critical Role of Prototyping and Quick Production in Electronic Appliance Development
The development of new electronic appliances is traditionally a costly and time-intensive process. However, contemporary approaches in the transition from concept to commercialization are transforming how these products are rolled out, focusing on enhancing efficiency and reducing expenses.
Rapid prototyping and manufacturing services offer a fast, reliable, and cost-effective means to develop prototype models that incorporate essential features and low-volume production parts. These services are crucial for validating concepts and conducting market tests on new electronic components and devices. This strategy allows for the testing of innovative ideas, the collection of early customer feedback, and the design of customized solutions that meet specific user requirements. These prototypes can be evaluated in controlled lab settings or through real-world usage, speeding up their readiness for market launch.
Additionally, this phase is instrumental in providing key insights into future production strategies, cost management, timeline optimization, and quality control measures. This not only helps in refining the product but also in streamlining the entire production process for electronic appliances.
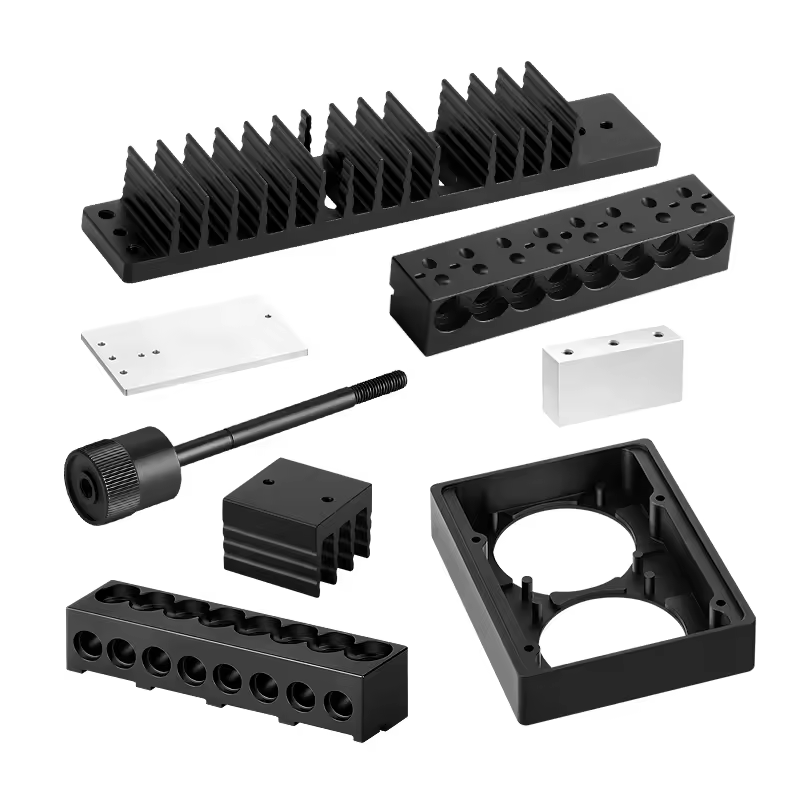
Optimizing Electronic Appliance Development Through Prototyping and Manufacturing
Proof of Concept:
Develop concepts for electronic appliances into a feasible scope, focusing on defining essential details and fully understanding the design intent through proof-of-concept prototypes.
Visual Presentation:
Visual presentation models enable designers to display the appearance and aesthetics of their electronic designs to colleagues, clients, and stakeholders, thereby encouraging clear and actionable feedback.
Functional Prototyping:
Functional prototyping in electronic appliance development, also known as Beta prototyping, allows for testing the form, fit, and function of components. This process aids in refining design iterations and improving product performance. It enables the early identification and resolution of issues, significantly reducing business risk before the product is finalized.
Engineering Validation:
Developing engineering prototypes that closely resemble the final electronic appliance simplifies the process of verifying design, engineering, and manufacturability. This step is essential before committing significant resources to costly tooling and production methods.
Pilot Production:
Rapid manufacturing and custom low-volume production of electronic appliances act as an effective bridge from prototype to full-scale production. This approach speeds up market entry and maintains cost-efficiency, facilitating a smoother transition to commercial availability.
Reach Out for Custom Electronic Appliance and Prototype Development
We specialize in delivering solutions for electronic appliance development, emphasizing manufacturability and cost-efficiency from the initial concept through to production.
Electronic Appliance Prototyping and On-Demand Manufacturing by AS Prototypes
With deep expertise, AS Prototypes excels in electronic appliance prototyping and machining, serving numerous manufacturers worldwide. We support you at every stage—from initial prototyping, through testing and iterations, to product demonstrations, and even into short or low-volume production runs.
Our prototyping and manufacturing capabilities are extensive, featuring an in-house CNC machining and finishing shop, 3D printing, urethane casting, rapid injection molding, and sheet metal fabrication to meet all your electronic appliance development needs.
CNC Machining for Electronic Appliances
CNC machining is a pivotal technology in the electronic appliance industry, enabling the precise and efficient production of complex components crucial for various electronic applications. At AS Prototypes, we specialize in CNC machining, using premium materials such as aluminum and stainless steel to meet strict specifications with high tolerances. This capability ensures that our machined parts, including appliance housings and structural components, meet the high-quality standards of the electronic sector.
Typical applications: Computer Enclosures, Heat Sinks, Connector Housings, Appliance Frames, Display Mounts, and Button Panels.
Typical materials: Aluminum, Stainless Steel, Polycarbonate, Acrylic, ABS, and PEEK.
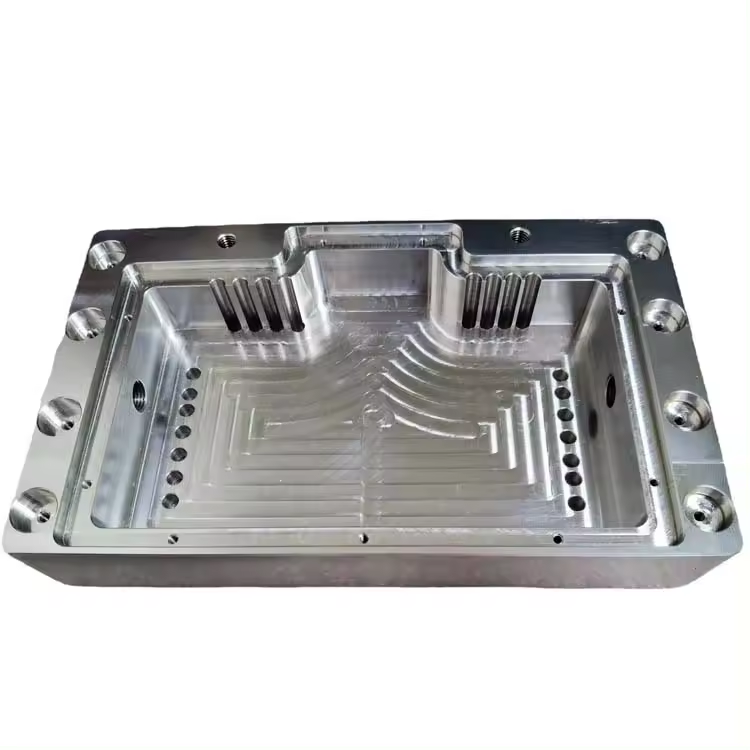
3D Printing for Electronic Appliances
3D printing is transforming the electronic appliance industry at AS Prototypes by enabling the rapid production of complex, customized components such as device-specific parts, advanced polymers, and precisely tailored electronic tools. We specialize in utilizing industry-grade materials to ensure each product not only meets precise specifications but also adheres to the high-quality standards required in electronic applications.
Typical applications: Enclosures for Electronics, Cooling Elements, Custom Mounts, Connector Housings, Protective Covers, Circuit Carriers, and Custom Knobs.
Typical materials: Polymers (ABS, PLA, PEEK), Polycarbonate, Nylon, Aluminum, Stainless Steel, and Composite Materials.
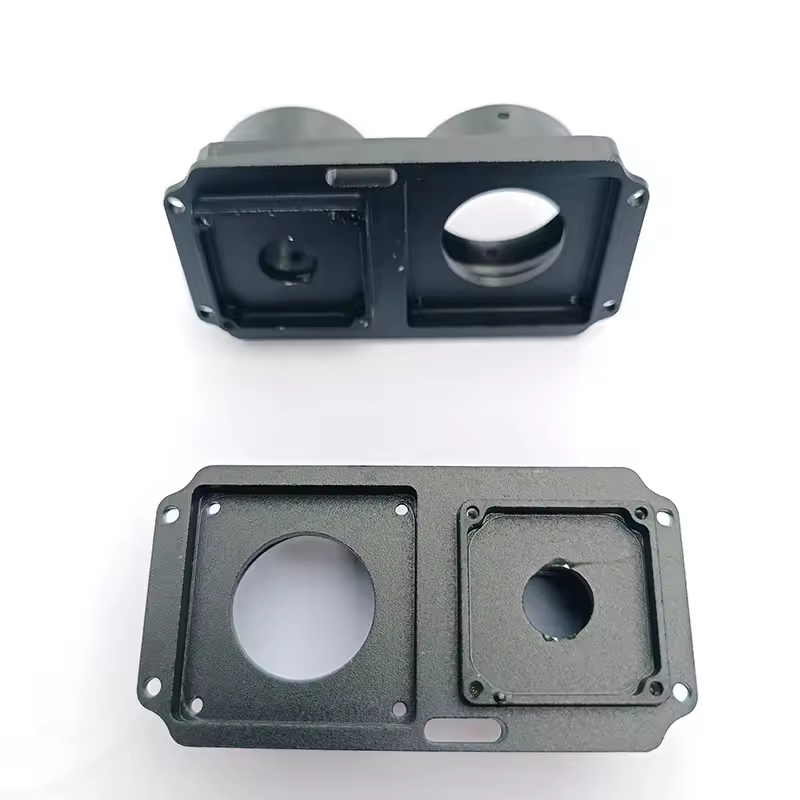
Contact Us for Custom Electronic Appliance Development and Prototyping
We specialize in providing solutions for electronic appliance development, focusing on manufacturability and cost-efficiency from the initial concept to production.
Vacuum Casting for Electronic Appliances
Polyurethane casting offers numerous benefits and applications, making it a valuable technique for the electronic appliance industry, particularly for low-volume production of electronic component housings. This method is ideal for initial product launches before investing in injection molding and tooling, allowing for market research and gathering customer feedback. It also facilitates the early delivery of electronic components. In markets characterized by rapid innovation and short product lifecycles, silicone molding used to cast urethane enables manufacturers to quickly iterate and refine their designs without the need to recoup the costs associated with hard tooling.
Typical applications: Enclosures for Electronics, Protective Covers, Appliance Models, Flexible Conduits, and Vibration Isolators.
Typical materials: Polyurethane, Epoxy Resins, Silicone, ABS-like Resins, High-performance Industrial-grade Resins.
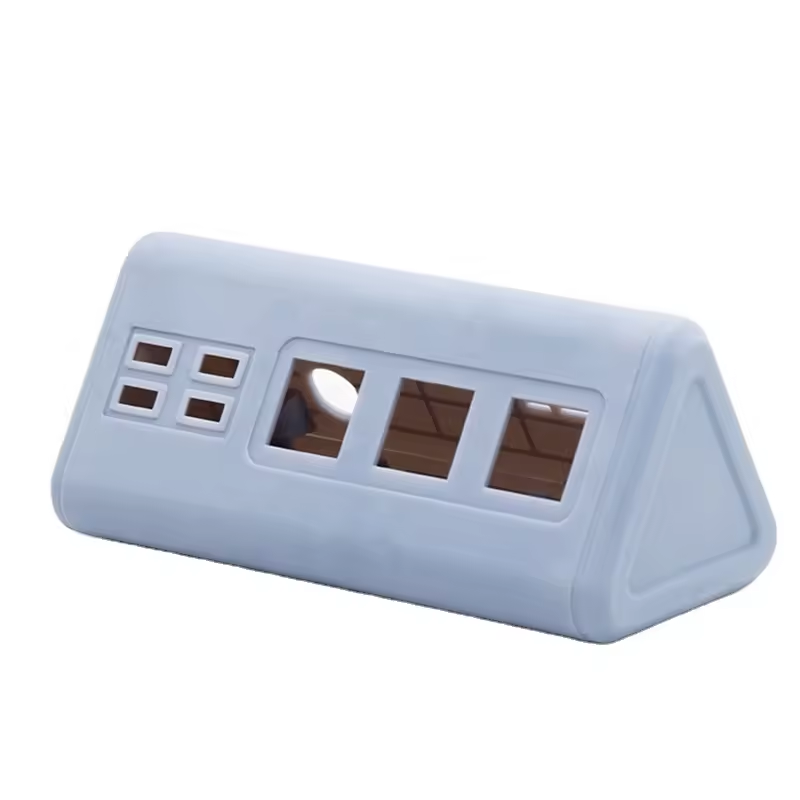
Rapid Injection Molding for Electronic Appliances
Rapid injection molding is an optimal solution for manufacturers of electronic appliances requiring low-volume molded parts. It effectively supports manufacturability analysis, engineering tests, product evaluations, investor demonstrations, and readiness for production in the advanced phases of electronic appliance development. Additionally, it serves as an intermediary between prototyping and full-scale production, allowing for the early detection and resolution of issues before transitioning to manufacturing.
Typical applications: Appliance Housings, Control Knobs, Ventilation Systems, Access Panels, and Battery Casings.
Typical materials: Polypropylene, Polycarbonate, Polyethylene, ABS, and PEEK.
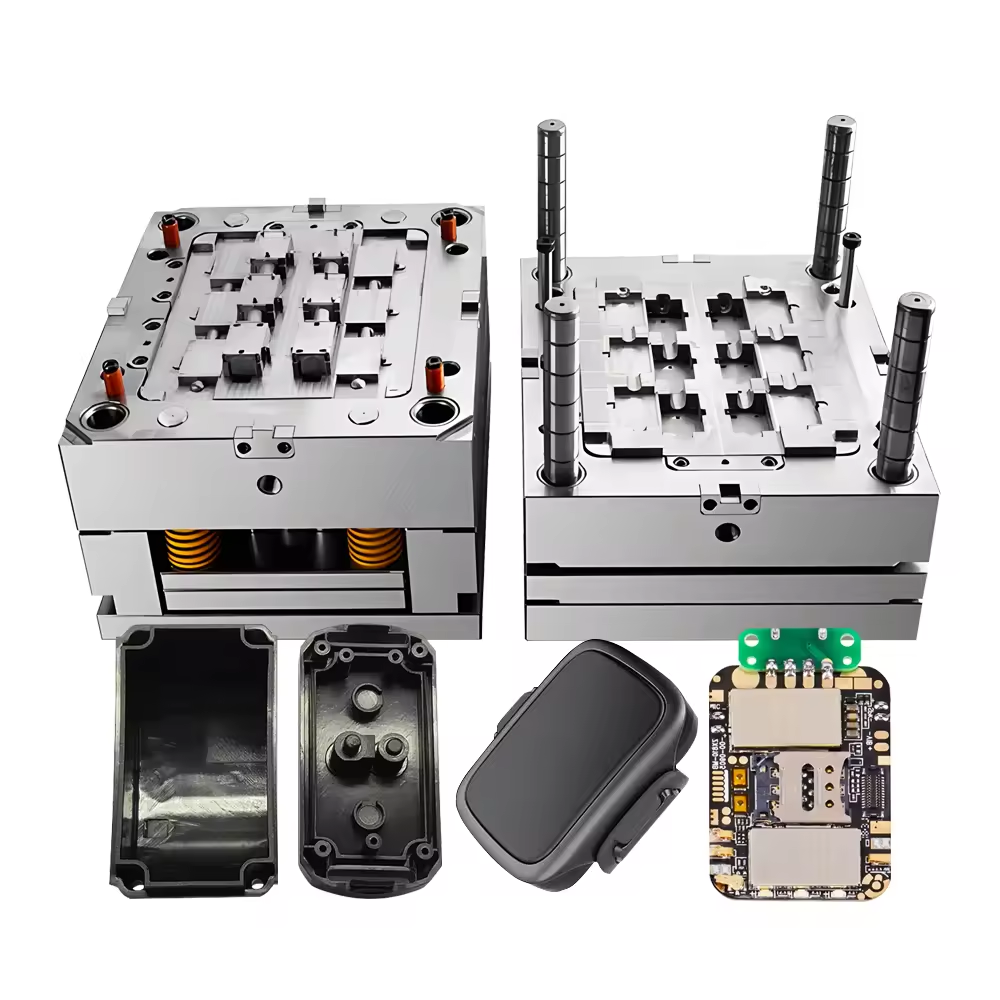
Sheet Metal for Electronic Appliances
Sheet metal fabrication is a crucial technique in the production of electronic appliance components, emphasizing precision and adaptability. This process involves cutting, bending, and assembling metal to create components for devices ranging from computer casings to enclosures for home appliances. The ability to meet exact specifications and maintain high tolerances makes sheet metal ideal for intricate electronic applications. Additionally, materials like aluminum used in this process are lightweight and offer excellent heat dissipation, which is essential for maintaining the performance and longevity of electronic devices.
Typical applications: Computer Casings, Appliance Frames, Heat Dissipation Panels, Protective Enclosures, and Mounting Brackets.
Typical materials: Aluminum, Stainless Steel, and Copper.
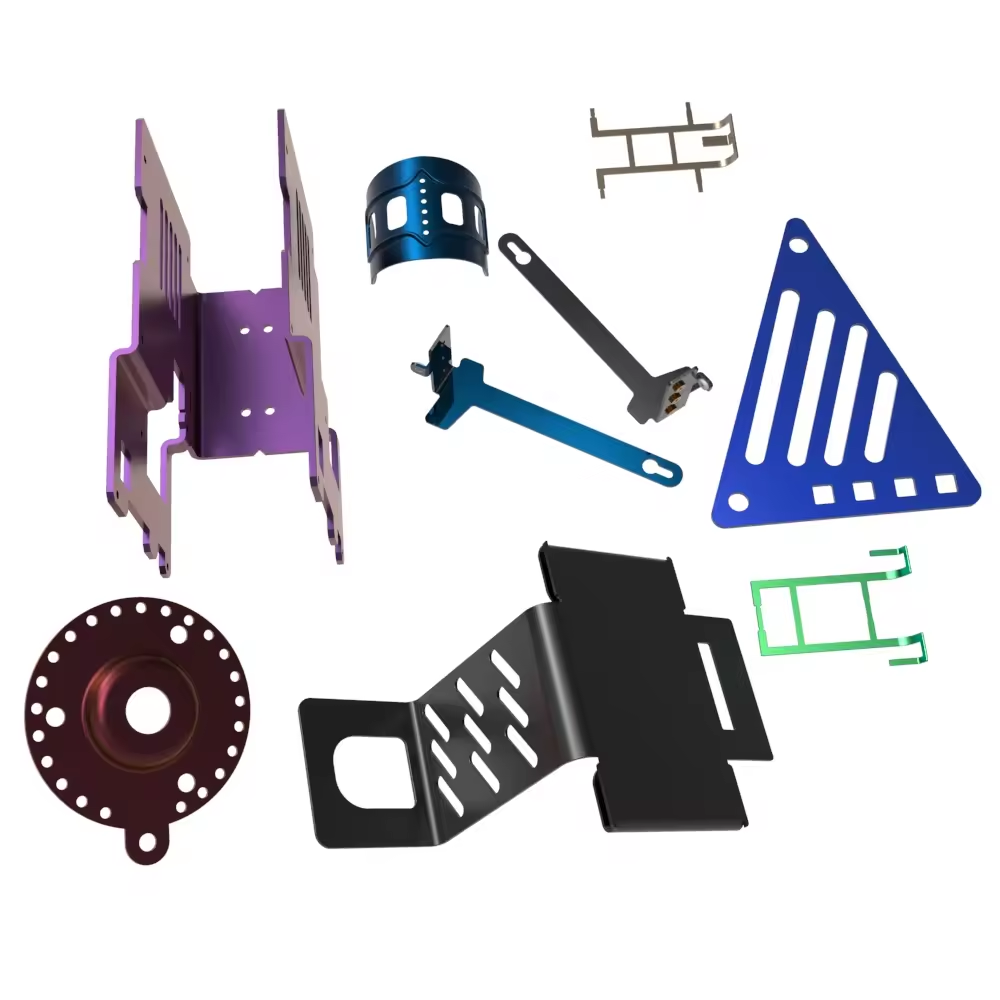
At AS Prototypes, we are committed to collaborating with you to ensure the success of your entire electronic appliance project. Whether you need prototypes, custom components, or mass-produced parts, we deliver reliable and consistent results, always adhering to your schedule.