The development of any product begins with its design. The conceptual design is then transformed into a physical prototype, which is a crucial step in the creation of new products or technologies. Physical prototypes are typically developed to assess and test the design by system analysts.
A physical prototype can range from a simple handmade model to a fully functional representation of how the conceptual design will perform in real-world conditions. Today, the manufacturing of physical prototypes has become more accessible due to the advent of various rapid prototyping techniques. These methods save time and reduce costs, allowing for the creation of numerous effective physical prototypes in a shorter period, while also appealing to customers with improved aesthetics and finishing.
Types of Physical Prototypes
1. Working Prototype
A working prototype is a type of physical prototype designed to embody all the features of the conceptual design. It is fully functional and accurately reflects how the product will perform under real-world conditions.
2. Visual Prototype
A visual prototype is a type of physical prototype created solely to represent the appearance, dimensions, and shape of the conceptual design. It is not meant to demonstrate the functionality of the design.
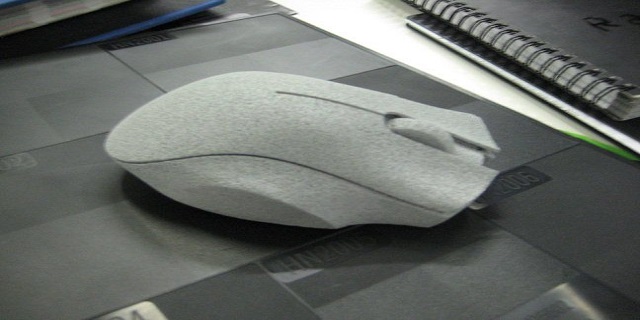
3. Functional Prototype
A functional prototype is akin to a working prototype, but it may be created using different scales and techniques than those used for the original product.
4. User Experience Prototype
A functional prototype is a type of physical prototype designed to provide sufficient information about the product being developed, which researchers can use for further investigation.
Rapid Prototyping: Development of Physical Prototypes
Prototype development is typically carried out using rapid prototyping techniques employed by manufacturers. These methods are both cost-effective and time-efficient. Additionally, the prototypes produced through these techniques are effective and visually appealing. Rapid prototyping is making significant strides in various industries, representing a revolutionary advancement. The fabrication of products is often accomplished through 3D printing or other additive manufacturing technologies, utilizing data from CAD models.
3D printing has emerged as a popular rapid prototyping technique, where material is solidified based on computer instructions derived from CAD model data to create the physical prototype. This method is gaining traction among both domestic and industrial users due to the readily available and affordable materials used in 3D printing compared to other manufacturing methods.
Modern modeling software is also facilitating rapid prototyping by saving CAD models in AMF format, which produces fewer errors than the traditional STL format. This software often features a user-friendly interface, making it easier for users to design their prototypes.
Manufacturers are also utilizing CNC (Computer Numerical Control) machines to convert conceptual models into physical prototypes. These machines operate using G-codes and M-codes for various manufacturing operations such as cutting, drilling, and boring. The CAD model is translated into manufacturing directives through CAM (Computer-Aided Manufacturing) software. This conversion process enables the machine to produce highly accurate physical prototypes. Today’s CNC machines, particularly 5-axis models, allow tools to move along five different axes simultaneously, resulting in the production of highly effective and precise components.
The primary distinction between 3D printers and CNC machines lies in the materials used for manufacturing. CNC machines are generally employed for creating metallic prototypes, while 3D printers typically utilize materials such as ABS, PLA, and soft PLA for physical prototype development. Furthermore, standard 3D printers occupy significantly less space compared to CNC machines, lathes, or precision grinding machines, making them a more suitable option for many manufacturers. Ultimately, the choice of rapid prototyping technique often depends on the specific material requirements for the physical prototype.
Other rapid prototyping techniques currently in use include:
Laminated Resin Printing (LRP)
Shape Deposition Manufacturing (SDM) (and Mold SDM)
Solid Ground Curing (SGC)
Selective Laser Sintering (SLS)
Selective Laser Melting (SLM)
Stereolithography (SLA)
Ballistic Particle Manufacturing (BPM)
Directed Light Fabrication (DLF)
Direct-Shell Production Casting (DSPC)
Fused Deposition Modeling (FDM)
Laminated Object Manufacturing (LOM)
Importance of Physical Prototype
The development of a physical prototype is essential prior to the creation of a product. A prototype serves to assess various aspects of the future product, as outlined below:
1. Determination of Production Cost and Issues
Developing a physical prototype before commencing actual production allows manufacturers to identify potential challenges that may arise during the manufacturing process. This proactive approach enables them to modify or eliminate any problematic operations, thereby minimizing production costs. Additionally, it helps manufacturers select the most efficient method for developing the product, ensuring it is both cost-effective and capable of producing accurate, error-free results.
2. Evaluation and Testing of Product
A conceptual design may differ from the final product, potentially leading to various issues for the manufacturer. This challenge can be addressed by initially creating a physical prototype using rapid prototyping techniques, allowing the conceptual design to be tested under real-world conditions. This process enables the manufacturer to assess all components and make necessary adjustments to the design. Additionally, each part can be evaluated and tested in practical scenarios, making it easier for the manufacturer to identify any challenges that may arise after the product is manufactured.
3. Sale of the Product
A physical prototype is more likely to attract customers compared to a simple design. With a prototype, customers can better understand the product, as it provides a tangible representation of its features and functionality. A functional prototype reveals hidden aspects of the product that may not be apparent in a design alone. Additionally, the enhanced aesthetics achieved through rapid prototyping techniques can significantly appeal to potential buyers. As a result, manufacturers can forecast product sales more accurately before actual production begins.
4. Patent
A new design or product can be more easily patented when a physical prototype is available. Having a prototype allows manufacturers to clearly identify which features of the design can be patented and which aspects may require modification to meet patentability criteria. This proactive approach helps protect manufacturers from potential lawsuits related to similarities with existing patented products. Furthermore, presenting a physical prototype to a patent attorney enables a more effective description of the key features, making the patent application process smoother compared to relying solely on a conceptual design.
Difference between a Prototype and Actual Product
While engineers and developers strive to minimize discrepancies between a prototype and the final product, some differences are often inevitable. These variations can occur in terms of the materials used, machining processes, and overall appearance.
Typically, the materials chosen for the final product are more expensive and challenging to fabricate. As a result, prototypes are usually constructed from materials that are easier to work with, yet possess properties similar to those of the final product. In some cases, the specific materials intended for the final product may not be available, necessitating the use of alternative materials for the prototype. Such differences can affect the appearance and finish of the final product compared to the prototype.
Final products are often manufactured in large quantities, which means the production methods may differ significantly. Mass production techniques that are cost-effective and time-efficient may not be suitable for prototypes due to material differences. Additionally, the fabrication processes for the final product can be quite complex, whereas prototypes are typically produced using simpler methods. This simplification can also lead to noticeable differences in the appearance of the final product versus the prototype.
Quality inspection techniques may also vary between prototypes and final products. The final product, intended for market sale, undergoes rigorous quality inspection tests. In contrast, physical prototypes are not subjected to the same level of scrutiny due to the differences in materials and manufacturing processes.
Conclusion
It is clear that developing a physical prototype is an essential process in today’s industries, allowing for the evaluation and testing of designs before moving into the manufacturing phase. Furthermore, a physical prototype helps predict manufacturing costs and identify potential challenges, enabling manufacturers to select the most cost-effective methods.
Additionally, a physical prototype is more appealing to customers than a conceptual design. With advancements in software and rapid prototyping techniques, producing a prototype has become quicker and more accurate. While there may be some differences between the prototype and the final product, the prototype plays a crucial role in enhancing product sales in modern industries.