Most products often require clear components or materials, and the level of clarity needed can be determined by the specific application of the optical prototype. Translucency in such parts is crucial, as it allows for the visibility of indicators, such as whether an LED is on or off. Key products that necessitate proper optical features include light pipes, displays, and lenses.
Various manufacturers specialize in producing clear prototype parts and can create custom parts tailored to your specifications. Techniques used in the production of clear custom parts include vacuum casting, injection molding, and rapid prototyping methodologies. The choice of method depends on the required level of clarity, timescale, quantities, and the complexity of the part. CNC machining is ideal for low-volume production of extremely clear prototype parts.
Hand polishing is often applied to materials like polycarbonate and acrylic to achieve the desired clarity standards. CNC machining offers an advantage over other additive manufacturing processes, where the layering must be smoothed out. Rapid prototyping provides different solutions, such as stereolithography, which can also produce clear parts when materials are mixed correctly. Overall, polycarbonate and acrylic machining are the best options for manufacturing clear prototype parts.
Production of Clear Acrylic Prototypes
Clear acrylic is a widely used material for rapid prototyping, favored by manufacturers globally. This type of plastic, commonly known as PMMA, is initially processed using computer numerical control (CNC) techniques. It is then transformed into clear acrylic prototypes, such as clear plastic prototypes or other clear rapid prototypes. The entire production process, from pouring to final product, typically takes about 3 to 7 days.
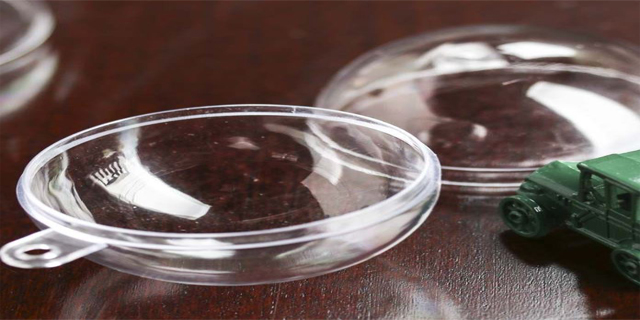
This approach helps minimize the production run and the required labor. Processes such as planting, silk screening, and polishing are typically performed before the material is applied to products. Each prototype part requires polishing after production to restore its true clarity. Without polishing, the machined part will remain translucent rather than completely clear. Clear acrylic prototypes are commonly used in the production of construction components such as flashlights, metal parts, and dashboards.
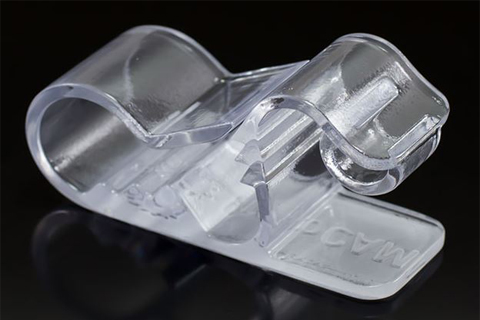
Why Acrylic?
Acrylic is an essential plastic for items that require transparency but do not need high impact resistance. One of the advantages of acrylic is its superior scratch resistance compared to other clear plastics. It serves as an excellent substitute for glass and is slightly cheaper than polycarbonate, particularly in applications where strength is not a critical factor. Advanced methods like laser cutting technology can reduce acrylic into very fine shapes, as the material vaporizes upon contact with intense laser energy.
Acrylic can be machined using CNC or crafted by hand. Any marks left on the item can be removed through polishing, which helps restore its optical clarity. Other products made from acrylic include lenses for magnifying glasses, replacement glass, fashion accessories like bracelets, and display items.
Characteristics of Acrylic
Acrylic is categorized as a thermoplastic due to its reaction to heat. Thermoplastics can be heated to their melting point, cooled, and reheated multiple times without significant degradation. Unlike thermoset plastics, which burn completely when reheated, thermoplastics like acrylic liquefy rather than burn, allowing them to be easily injection molded and later recycled.
In contrast, thermoset plastics can only be heated once during the injection molding process. The initial heating causes chemical changes that are irreversible, and reheating them will result in complete burning, making them non-recyclable.
Acrylic boasts a bright and shiny exterior and has a high longevity of about ten years, maintaining its durable colors. Its vibrant and appealing appearance makes it a preferred choice for many customers.
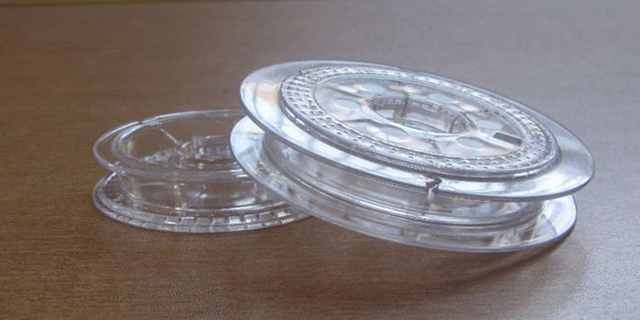
Acrylic also boasts higher strength performance compared to other ordinary plastics. Acrylic prototypes exhibit stable characteristics in terms of heat resistance and strong physical performance. However, poor manufacturing can lead to stress cracks or breakage over time. As a robust plastic, acrylic can withstand high temperatures without distorting. It can also be processed using various manufacturing procedures such as drilling, sawing, or cutting.
Acrylic is available in round stock or sheet stock, making it an ideal material for subtractive machining procedures on different tooling machines. It comes in a broad range of colors, including various fluorescent options. While the colors of the layers may not be immediately obvious, they become visible at the edges, giving the material a brightened appearance even without a direct light source.
Prototype Development Using Acrylic
Parts manufactured from clear acrylic stock should have tool marks removed through polishing or sanding to fully restore the material’s transparency. Acrylic sheets can be efficiently heated and shaped as needed. Simple curves can be achieved by heating the curved point with a special heating wire, while entire sheets can be heated and molded into desired designs. Acrylic parts created from different pieces can be seamlessly joined using liquids that melt both surfaces, resulting in nearly invisible joints.
Acrylic is also available as a filament for three-dimensional printing, typically in black, white, or transparent forms. Importantly, acrylic is non-toxic and does not release harmful substances, even when in contact with water. This contrasts with polycarbonate, which releases bisphenol A, a hazardous material. By choosing acrylic, you can enjoy its numerous benefits without the associated health risks.