Today, we’ll explore the manufacturing processes of acrylic polymers, with a focus on CNC acrylic machining. Acrylic is one of the most widely used plastics globally, competing closely with glass and polycarbonate. Its versatility across various industries makes understanding its manufacturing processes valuable, especially CNC machining, which is integral to acrylic production. This guide will help you select the right blank, cut, and engrave it using CNC routers, and outline the steps to take after cutting.
The Advantages of Acrylic and Why Machining is Ideal
Acrylic is favored for its remarkable properties. It is five times stronger than glass, meaning it is highly shock-resistant and shatterproof. Acrylic offers 92% transparency, surpassing window glass (83-90%) and on par with polycarbonate (90%). Unlike other plastics, acrylic does not degrade under prolonged UV exposure—while polycarbonate may yellow, and others become brittle. Acrylic is also corrosion and water-resistant.
These properties make acrylic parts durable, resistant, and transparent, ideal for applications like car lights, signage, light tubes, and more. These uses demand precision and a superior surface finish, making CNC machining an optimal choice due to acrylic’s strength and rigidity.
Choosing the Right Acrylic for CNC Machining
Acrylic blanks are produced through extrusion or casting. Extrusion is primarily for sheets, while casting can produce sheets and various forms. Thicknesses range from 1.5 to 25 mm, making acrylic suitable for flat emblems and signs. But, which type of blank is better for CNC cutting?
Extruded acrylic involves melting pellets and pushing them through a nozzle, while casting involves pouring melted pellets into a mold. Extruded acrylic tends to be more brittle and anisotropic, making it less suitable for machining. Cast acrylic, on the other hand, is more uniform and less prone to cracking, making it the better choice for CNC machining.
Fixing Acrylic Parts for Machining
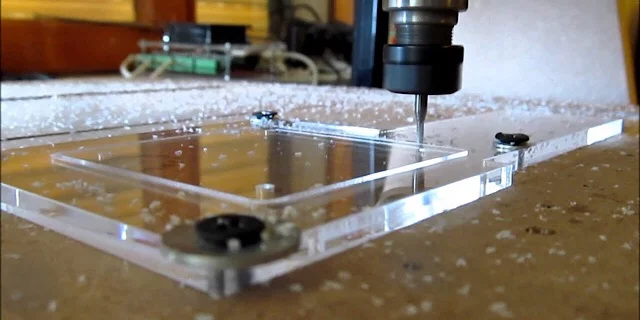
After selecting the appropriate blank, securing it is crucial. Any metal or plastic CNC router can handle the job, but avoid wood routers due to their lack of rigidity. Clamping methods depend on the blank size. Smaller pieces can be clamped with jigs and vises, while larger sheets might require gluing, taping, or vacuum tables to ensure stability.
Machining Acrylic: Techniques and Tips
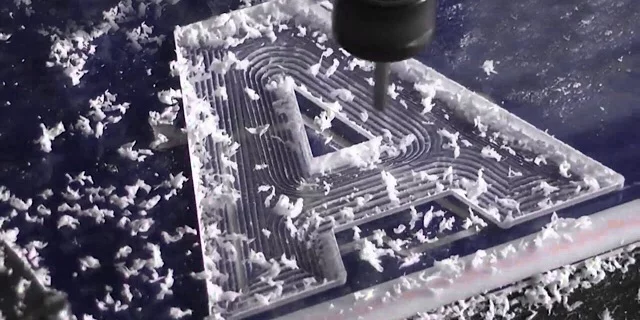
Feed Rates
When machining acrylic, a stable and aggressive feed rate is necessary to prevent heat buildup from friction. This helps avoid chips welding back onto the part, which would compromise surface finish and precision. Use a spindle speed of 15,000-18,000 RPM.
Cutting Tools
Specialized cutting tools are essential. Acrylic cutting bits with optimized flutes ensure precise chip removal. For drilling, use a drill with a tip angle of 60 degrees instead of the standard 120 degrees for better chip clearance.
Coolants
Maintaining a low temperature during CNC cutting is crucial. Cooling acrylic sheets before machining can enhance chip removal. If using coolants, ensure they don’t react with PMMA.
CNC Acrylic Engraving
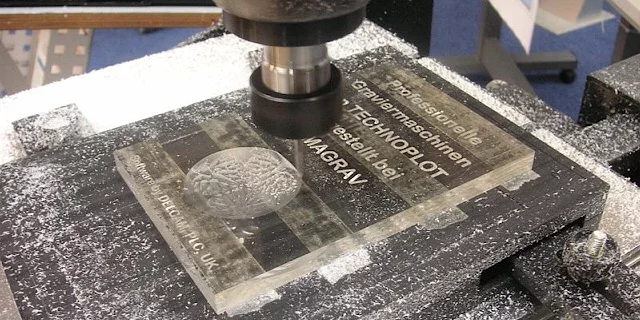
Engraving is similar to milling but uses different tools. This method is popular for creating intricate designs on acrylic for aesthetic or advertising purposes. The grooves can be filled with paint to enhance visibility.
Post-Processing Machined Acrylic
After achieving the desired shape and precision, acrylic parts need grinding and polishing. This involves using progressively finer polishing tools and a linen towel with polishing paste. Chemical polishing, involving special gases, can also be used to melt the surface layer. Advanced techniques like diamond tool single-tip milling can achieve a high-quality finish.
Our Expertise in CNC Machining Acrylic
As a leading prototype manufacturer, AS Prototypes excels in producing clear acrylic optical components using 3-axis, 4-axis, and 5-axis CNC machines. We employ cutting-edge diamond machining technology, such as SPDM or SPDT, to achieve ultra-precise manufacturing of lenses and light guides with exceptional optical quality.
Looking ahead, we aim to enhance our CNC prototyping services by upgrading equipment and tools to deliver the highest quality machined plastic parts. Our mission is to provide outstanding service for machining complex optical components in any required shape.