Insert molding is a specialized manufacturing technique that integrates different materials, typically metal and plastic, into a single molded part. At AS Prototypes, we leverage this process to produce robust, lightweight, and multifunctional components, widely applicable across various industries.
What is Insert Molding?
At its core, insert molding involves placing an insert — often made of metal — into a mold, which is then filled with molten plastic. This forms a unified part where the insert is encapsulated by the plastic. This method is particularly beneficial for creating parts that combine the strength of metal with the design flexibility and aesthetics of plastics.
Materials Used in Insert Molding
The choice of materials in insert molding is crucial, as it impacts the durability and functionality of the final product. At AS Prototypes, we commonly use:
- Thermoplastics: Such as Polypropylene (PP), Nylons (PA), Polycarbonate (PC), ABS, Polyethylene (PE), and Acetal.
- Thermosets: Including Polyester, Epoxy, and melamine-formaldehyde resins.
- Elastomers: Like Polyurethane and natural rubber.
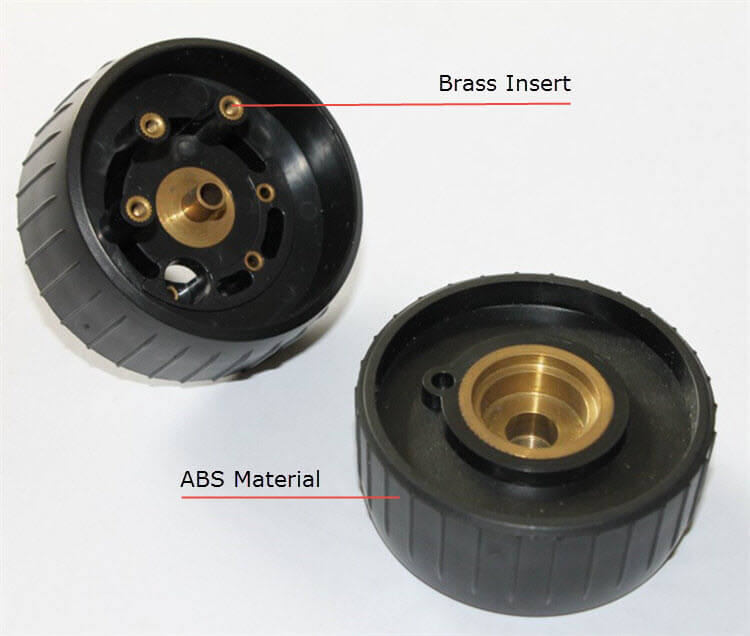
The Insert Molding Process at AS Prototypes
Our insert molding process is meticulous and structured to ensure precision and quality:
- Insert Loading: Depending on the volume and complexity, we employ either automated mechanisms for high precision and efficiency or manual insertion for low-volume productions, allowing careful placement and inspection.
- Injection of Molten Plastic: We use state-of-the-art injection units to inject molten plastic into the mold, ensuring a tight bond between the insert and the plastic.
- Cooling and Ejection: After the plastic has solidified, the mold is opened, and the part is carefully ejected, maintaining the integrity of the embedded insert.
- Post-Processing: This includes deburring, heat treatment, and humidity control to enhance the quality and durability of the part.
Design Considerations in Insert Molding
Designing for insert molding requires careful consideration of several factors to ensure part efficacy and manufacturability:
- Cost Efficiency: We analyze the cost implications of each design to ensure it meets budgetary constraints without compromising quality.
- Insert Properties: The choice of insert material is critical, as it must withstand the molding process’s high temperatures and pressures.
- Insert Placement: Strategic placement of inserts is crucial to withstand operational stresses and maintain part functionality.
- Material Compatibility: We select compatible materials for the insert and the surrounding plastic to ensure a strong bond and minimize defects.
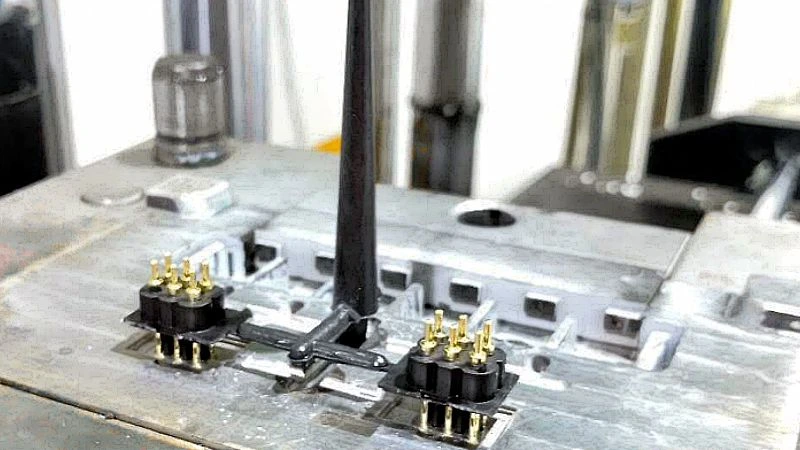
Advantages of Insert Molding with AS Prototypes
Insert molding offers numerous advantages, making it a preferred choice for many applications:
- Integrated Design: Reduces assembly time and costs by combining multiple components into a single molded part.
- Enhanced Strength and Functionality: Metal inserts enhance the mechanical properties of plastic parts.
- Design Flexibility: Allows for complex and custom shapes that are otherwise challenging to achieve.
Applications Across Industries
Our insert molded parts find applications in diverse sectors:
- Automotive: For components like sensors and knobs that require durability and precision.
- Consumer Electronics: In devices where compact and reliable integration of parts is crucial.
- Medical Devices: Where sterilization and durability are paramount.
Choose AS Prototypes for Expert Insert Molding Solutions
At AS Prototypes, we are dedicated to providing advanced insert molding solutions that meet the high standards of functionality and durability required by modern industries. Our expertise in handling complex insert molding projects ensures that we deliver not just parts but partnerships in innovation and efficiency. Contact us to explore how our insert molding capabilities can enhance your next project.