Rudgley M describes rapid manufacturing as the process of creating final, functional products using additive manufacturing techniques. This method leverages prototype manufacturing technology to produce the desired items for production. Rapid manufacturing represents an evolution of rapid prototyping technology, though there are still numerous areas that require enhancement.
The primary technologies used in prototype manufacturing are SLA (Stereolithography), SLS (Selective Laser Sintering), and FDM (Fused Deposition Modeling). A common characteristic of these technologies is that they decompose the part into individual layers and construct each layer independently.
Complex Geometry
One of the most attractive features of rapid prototyping products is their virtually unlimited geometric flexibility. This process allows for the creation of items with significant independence and freedom in design, including inverted concave shapes, overhangs, freeform structures, and various basic geometric configurations. For instance, the SLS (Selective Laser Sintering) process does not require support structures, enabling parts to be positioned in any orientation during machining without the need for clamps. This capability grants SLS the potential to achieve nearly infinite geometric possibilities for the workpiece.
Additionally, rapid prototyping technology can produce a wide range of products, from micro-sized to large-scale items. The size of the product is determined by the chosen process: SLS, SLA (Stereolithography), and FDM (Fused Deposition Modeling) are typically used for manufacturing medium-sized parts due to considerations of process execution, economic cost, and the performance of larger parts. However, these processes face limitations when it comes to producing very large products.
Unlike conventional processing methods that require molds, polymer rapid prototyping technology allows for the creation of custom-defined products more economically. This cost-effectiveness, combined with the ability to achieve complex geometries, makes rapid prototyping particularly advantageous in the medical field. Moreover, the high geometric flexibility of rapid prototyping also facilitates its integration with traditional manufacturing methods, emerging as a key development direction in today’s rapid prototyping technology. For example, the production of thin-walled, long, and narrow parts, previously achievable only with the EMD (Electro-Sparking) process, can now be efficiently accomplished using rapid prototyping, providing a comprehensive solution for such manufacturing needs.
DLM & Reverse Engineering
With the rapid prototyping process, parts featuring complex geometries—such as concave shapes, inner sharp corners, and long thin walls—that are difficult or impossible to machine using conventional methods can be easily manufactured. However, to fully leverage the capabilities of RP technology, designers need to rethink their approach to part design, embracing the freedom these processes offer.
It is important to note that the realization of these free design capabilities requires further development of specialized CAD software tailored for RP technology. Enhancements in design tools, combined with a shift in designers’ conceptual approaches, can unlock the full potential of rapid prototyping.
In addition to creating models of new products, engineers often use existing physical designs as a basis, a practice known as reverse engineering. Rapid detection and 3D CAD reconstruction technologies facilitate this by enabling the direct acquisition of CAD models from physical objects.
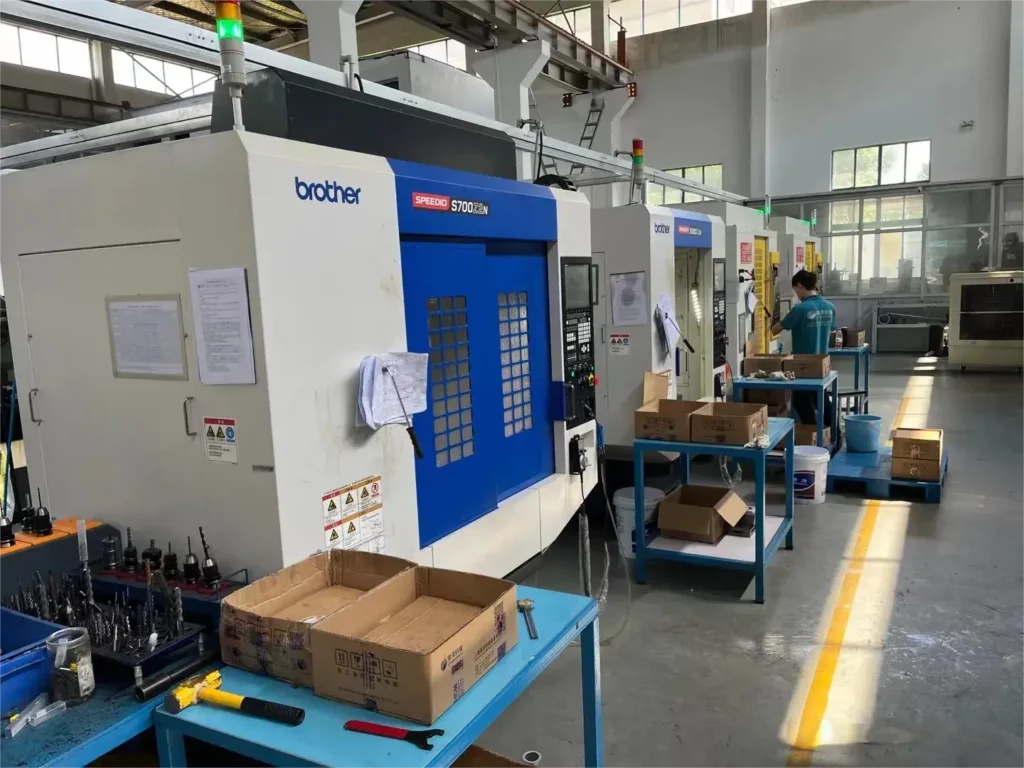
Speedability
Rapid prototyping technology earns its name due to its significantly shorter production cycle compared to traditional processing methods. One of its key advantages is its low sensitivity to design changes, meaning it offers a high degree of flexibility in production. This flexibility allows manufacturers to largely disregard shape constraints during the manufacturing process, thereby saving considerable time.
As a result, many companies utilize RP technology to create test pieces of products. This enables them to quickly assess the performance and other parameters of the product, facilitating faster iteration and development.
Economics & Other Constraints
Despite advancements in the productivity of various rapid prototyping (RP) processes, they still fall short of meeting the production requirements for large-scale manufacturing. Additionally, the inherent variability and precision of RP processes can result in significant equipment and material losses.
Currently, RP technology offers substantial advantages for product prototyping and trial production. However, the high cost of equipment, material wastage, and productivity gaps compared to traditional manufacturing methods hinder its widespread adoption for mass production. Economic considerations are just one of the reasons RP processes are seldom used for producing long-lasting parts. Other critical factors include product strength, material properties, and process repeatability.
The Development Of Prototype Manufacture Technology
In the current state of rapid prototyping (RP) technology, there remains a gap between the quality of products manufactured using RP and those produced by traditional manufacturing methods, particularly in terms of surface roughness, precision, repeatability, and overall product quality. To bridge this gap, the existing RP processes and process chains will need to undergo significant development to achieve the reliability and safety required for high-precision and high-quality production.
At present, the precision (0.1-0.2 mm per 100 mm) and surface roughness (Ra 5-20 μm) of RP processes are similar across different technologies, but the repeatability is relatively low. Enhancements in mechanical design, potentially facilitated by a technical feedback system, are necessary to improve these aspects. It is foreseeable that achieving higher product quality will involve the development of composite process equipment that combines RP processes with traditional manufacturing methods.
From the perspective of equipment and materials, the primary research directions focus on processing methods, processing equipment, laser generators, and materials. The goal is to improve the strength, durability, precision, and production cycle of RP-manufactured products. These advancements will ultimately drive the transition from rapid prototyping to rapid manufacturing, providing a powerful impetus for the evolution of the technology.
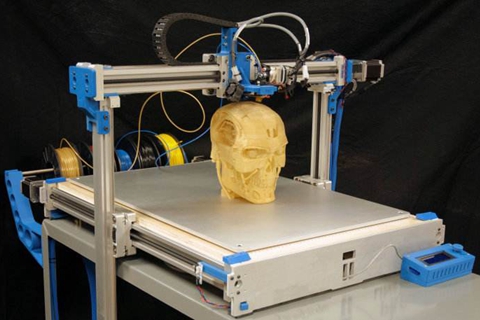
In the realm of component manufacturing, 3D printing technology enables the rapid production of complex products. In traditional automobile manufacturing, the development of automotive parts typically requires extensive research and development, as well as thorough verification. This process involves creating part molds, which is both time-consuming and costly. Any issues that arise necessitate modifications to the part structure, further extending the development cycle.
In contrast, 3D printing technology allows for the swift creation of intricate parts. If a problem is identified during testing, the 3D file can be quickly modified and the part reprinted for further testing. This capability significantly reduces both the cost and time associated with developing new parts, making the process more efficient and economical.